страница 1
Министерство образования и науки Республики Казахстан
Павлодарский государственный университет
им. С. Торайгырова
Факультет металлургии, машиностроения и транспорта
Кафедра машиностроения и стандартизации
КИНЕМАТИЧЕСКАЯ СТРУКТУРА И НАСТРОЙКА ЗУБОСТРОГАЛЬНОГО ПОЛУАВТОМАТА МОД. 5236П
Методические указания к выполнению лабораторной работы № 7 по дисциплине «Металлорежущие станки» для студентов машиностроительных специальностей
(для внутривузовского пользования)
Павлодар
УДК 621.9.06(07)
ББК 34.63-5я7
К41
Рекомендовано Учёным советом ПГУ им. С. Торайгырова
Рецензенты:
кандидат технических наук, профессор Дудак Н.С..
Составители: И.А. Шумейко, Р.О. Олжабаев, Д.А. Искакова
К41 Кинематическая структура и настройка зубострогального полуавтомата мод. 5236П: методические указания к выполнению лабораторной работы № 7 по дисциплине «Металлорежущие станки» для студентов машиностроительных специальностей (для внутривузовского пользования). Павлодар, 2007. 43 с.
В методическом указании изложен принцип получения зубьев конического зубчатого колеса, на основе которого составлена структурная и, далее, кинематическая схема станка. На основе кинематической схемы изложена методика расчета и настройки параметров движений. Акцентировано внимание на особенностях зубострогального полуавтомата для обработки конических зубчатых колес методом обката.
Лабораторная работа является составной частью общего цикла лабораторных работ, предусмотренных по дисциплине «Металлорежущие станки».
УДК 621.9.06(07)
ББК 34.63-5я7
©Шумейко И.А., 2007
©Павлодарский государственный университет
им. С. Торайгырова, 2007
Введение
Конические зубчатые передачи находят широкое применение в машиностроении. Изготовление высококачественных конических колес является весьма сложной задачей. Сложность ее, прежде всего заключается в том, что производящий режущий инструмент, представляющий собой кольцевую рейку, является воображаемым плоским колесом. Все расчеты же и наладка станка производятся как с реально существующим плоским производящим колесом. Кроме того, помимо формообразующих движений с участием упомянутого производящего колеса, на станке одновременно имеют место все остальные исполнительные движения характерные для металлорежущих станков, а именно, движения врезания, деления и вспомогательные.
В методическом указании ставится цель ознакомить студентов с принципом нарезания конических зубчатых колес методом обката и на этой основе привить студентам практические навыки расчета параметров, настройки и наладки станка на обработку конического зубчатого колеса на конкретном зубострогальном полуавтомате.
1 Цель и задачи лабораторной работы
1.1 Цель лабораторной работы – изучить принцип работы зубострогального полуавтомата для обработки конических зубчатых колес, произвести расчеты, настройку и наладку станка.
1.2 Задачи лабораторной работы:
1) Изучить настоящее методическое указание.
2) Получить индивидуальное задание и с помощью преподавателя или учебного мастера в лаборатории ознакомиться со станком.
Примечание: в связи с большим объемом работ по настройке и наладке станка и сложностью их выполнения студенты производят настройку и наладку лишь отдельных элементов согласно одному из вариантов, указанному учебным мастером.
3) Выполнить эскиз детали по варианту (приложение В) с указанием всех размеров и требований, предъявляемых к зубчатому колесу; из приложения Б выписать все параметры, характеризующие нарезаемое коническое зубчатое колесо согласно варианту.
4) Произвести расчет и анализ параметров по кинематической группе создающей движение скорости резания Фυ(П1); освоить методику наладки режущего инструмента.
5) Произвести расчет и анализ параметров по кинематической группе создающей движение обката Фs(B2B3); выполнить настройку кинематической цепи и установку исходного положения.
6) Произвести расчеты по кинематической группе создающей движение Д (B4) и выполнить установку органа настройки.
7) Выполнить операции по обеспечению требуемого движения врезания (осевая, угловая установка бабки изделия и установка стола).
8) Обработать зубчатое колесо по одному из вариантов.
9) Составить циклограмму работы зубострогального полуавтомата.
2 Назначение и техническая характеристика зубострогального полуавтомата мод. 5236 П
Станок предназначен для нарезания методом обката прямозубых конических колес диаметром до 125 мм и модулем до 2,5 мм. Он работает двумя зубострогальными резцами (ГОСТ 5392-64) из быстрорежущей стали Р9К10.
Станок может быть применен при любом характере производства. Однако, целесообразнее использовать его в условиях мелкосерийного производства.
Техническая характеристика
Наибольший модуль нарезаемых колес, мм 2,5 мм
Наибольший диаметр делительной окружности
нарезаемого колеса 125 мм
Длина образующей делительного конуса
наибольшая 63 мм
наименьшая 7 мм
Наибольшая ширина зубчатого венца 20 мм
Число двойных ходов суппортов в минуту
наибольшее 630
наименьшее 160
Число скоростей 7
Мощность привода главного движения 1,1 кВт
Мощность привода подачи 1,5 кВт
Мощность привода гидравлики 1,5 кВт
3 Принцип нарезания зубьев на зубострогальных полуавтоматах типа 5236 П
В качестве производящего элемента (режущего инструмента) используется плоское производящее колесо (ППК).
Плоское производящее колесо – это коническое зубчатое колесо с углом начального конуса 2 = 1800 (рисунок 1,а). В зацеплении конических зубчатых колес оно имеет такое же значение, как зубчатая рейка в зацеплении цилиндрических колес и является кольцевой рейкой для конических колес. Кольцевая рейка является предельным коническим колесом (2 = 1800) в том же смысле, в каком прямолинейная зубчатая рейка представляет собой предельное цилиндрическое колесо с радиусом R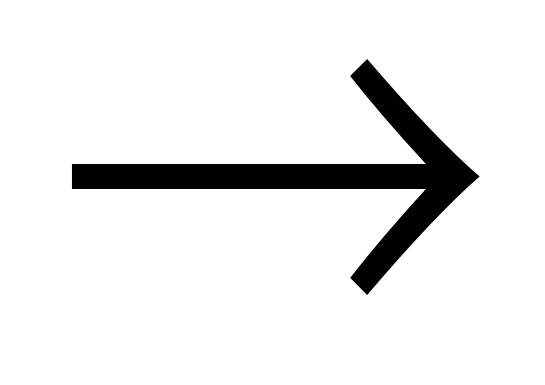 .
Рисунок 1
Радиус плоского колеса Rс зависит от длины образующей начального конуса сопряженного колеса. В процессе обката нарезаемого колеса по плоскому образующие начальных конусов этих колес практически совпадают. Следовательно, можно записать, что Rc = L, где L – длина образующей начального конуса нарезаемого колеса. Выразив их через модуль и число зубьев, получим:
= ,
откуда
zc = 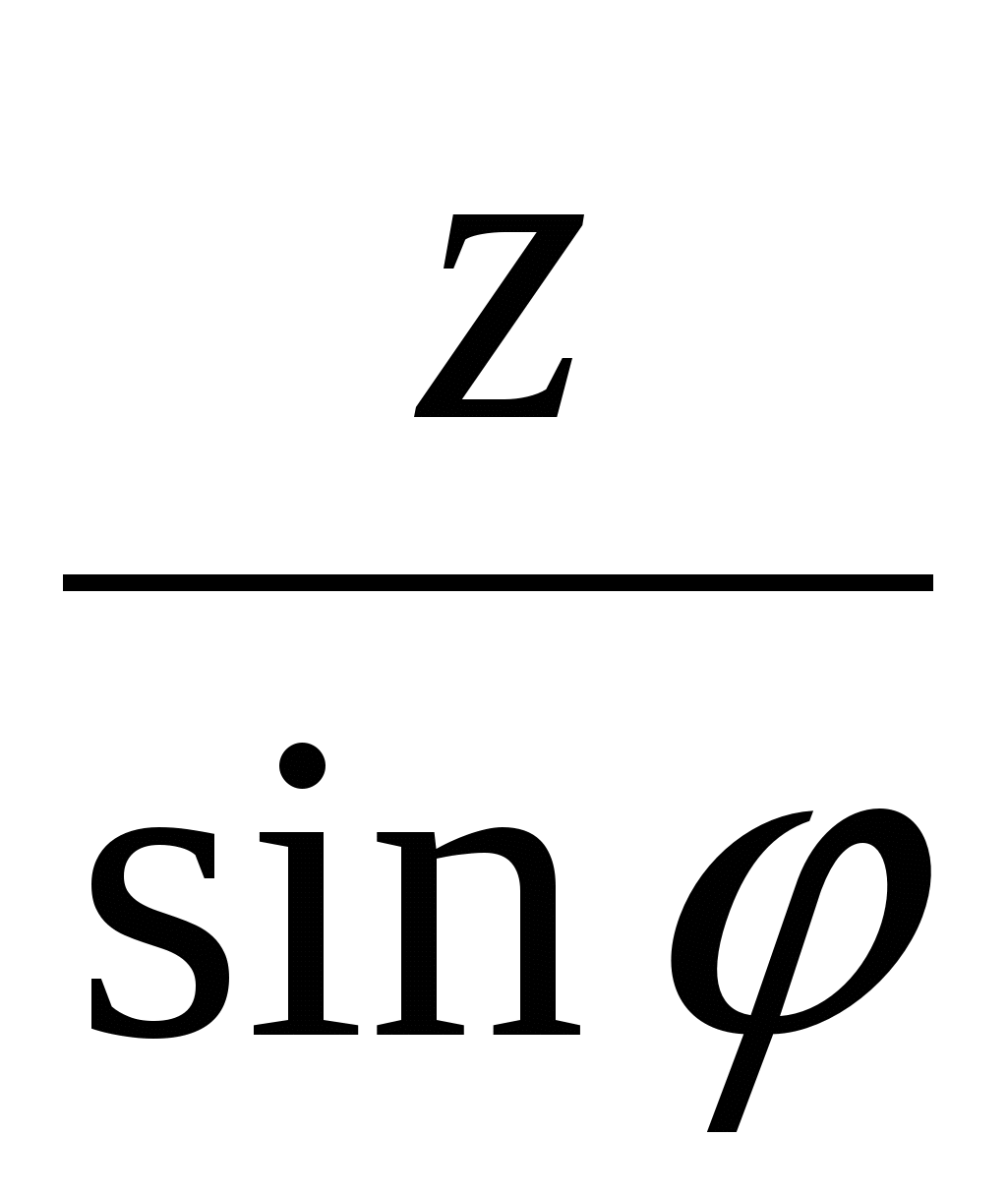
где zc – расчетное число зубьев ППК (рассчитывается с точностью до пятого знака);
z – число зубьев нарезаемого колеса или шестерни (ведущее зубчатое колесо считается шестерней, ведомое – колесом).
Если угол между осями двух сопряженных конических зубчатых колес с числом зубьев Zш и Zк шестерни и колеса ∑ = 900, то число зубьев плоского производящего колеса определяется из выражения:
Zc = .
У плоского производящего колеса производящие поверхности зубьев образуются движением прямолинейных режущих кромок двух строгальных резцов, работающих в соседних впадинах нарезаемого колеса (рисунок 1,б). Кромки резцов расположены так, что профиль зубьев производящего колеса совпадает с профилем исходного контура кольцевой рейки. При обкате по ППК условно мягкой заготовки (рисунок 2) на ней будут выдавливаться зубья с эвольвентным профилем.
Рисунок 2
Направляющая производящая линия (профиль зубьев) получается методом обката движением обкатной подачи Фs(В2 В3), где В2 вращение ППК, а В3 согласованное с ним вращение заготовки. Образующая производящая линия (форма зуба по длине) получается методом следа реализуемого движением скорости резания Фv(П1), где П1 поступательное перемещение резцов вдоль образующей конуса впадин нарезаемого конического зубчатого колеса. Таким образом, кинематическая структура станка комбинированная К23. В состав первой кинематической группы, создающей простое движение скорости резания Фv(П1), входят внутренняя связь (направляющие суппортов резцов), внешняя связь с органом настройки ίv (рисунок 3) и источник движения М1. В состав второй кинематической группы, создающей сложное движение обкатной подачи Фs(В2В3), входят внутренняя связь с органом настройки ίх, внешняя связь с органом настройки ίs и источник движения М2. В связи с тем, что ППК имеет только один зуб, существующий в виде перемещающихся режущих кромок резца, то после нарезания очередного зуба на заготовке ППК необходимо возвращать в исходное положение. С этой целью во внутреннюю связь второй кинематической группы встроен реверс Р. Для управления циклом работы станка используется распределительный вал (РВ) с кулачками К1, К2, К3, К4.
Рисунок 3
Кроме того, для нарезания последующих зубьев необходимо производить делительный поворот заготовки Д (В4). Для обеспечения точного деления во внутренней связи кинематической группы, создающей движение обката, имеется орган настройки ίd.
На основе рассмотренной структуры разработана кинематическая схема зубострогального полуавтомата мод. 5236П (рисунок 4), которая будет использована для определения значений параметров движений.
4 Расчет параметров, настройка и наладка станка
4.1 Кинематическая группа, создающая движение скорости резания Фv (П1)
Это движение простое с незамкнутой траекторией, поэтому необходимо настроить четыре параметра: скорость, направление, путь и исходное положение.
1) Траектория (прямая линия) не настраивается, т.к. обеспечивается прямолинейными направляющими суппортов с блоками резцов.
2) Настройка скорости резания ( внешняя связь).
Частота двойных ходов рассчитывается по формуле:
n = дв. ход./ мин.
где V – скорость резания, которая принимается равной 10 – 12 м/мин при обработке зубьев конических колес из стали (более низкие скорости при обработке колес из легированной стали);
b – ширина зубчатого венца, мм;
– перебег резцов, принимается равным 8 мм, причем со стороны утолщенного конца зуба рекомендуется выход резца – 5 мм, а со стороны тонкого конца – 3 мм.
При обработке зубчатых колес из цветных металлов скорость резания можно принять равной V = 12 м/мин. Определение формулы настройки для достижения расчетной частоты двойных ходов резцов:
Условие настройки: nэ об/мин → n дв. х. резцов/мин,
где nэ – частота вращения ротора электродвигателя главного движения, об/мин.
Уравнение кинематического баланса (УКБ) (рисунок 4):
Рисунок 4
nэ ∙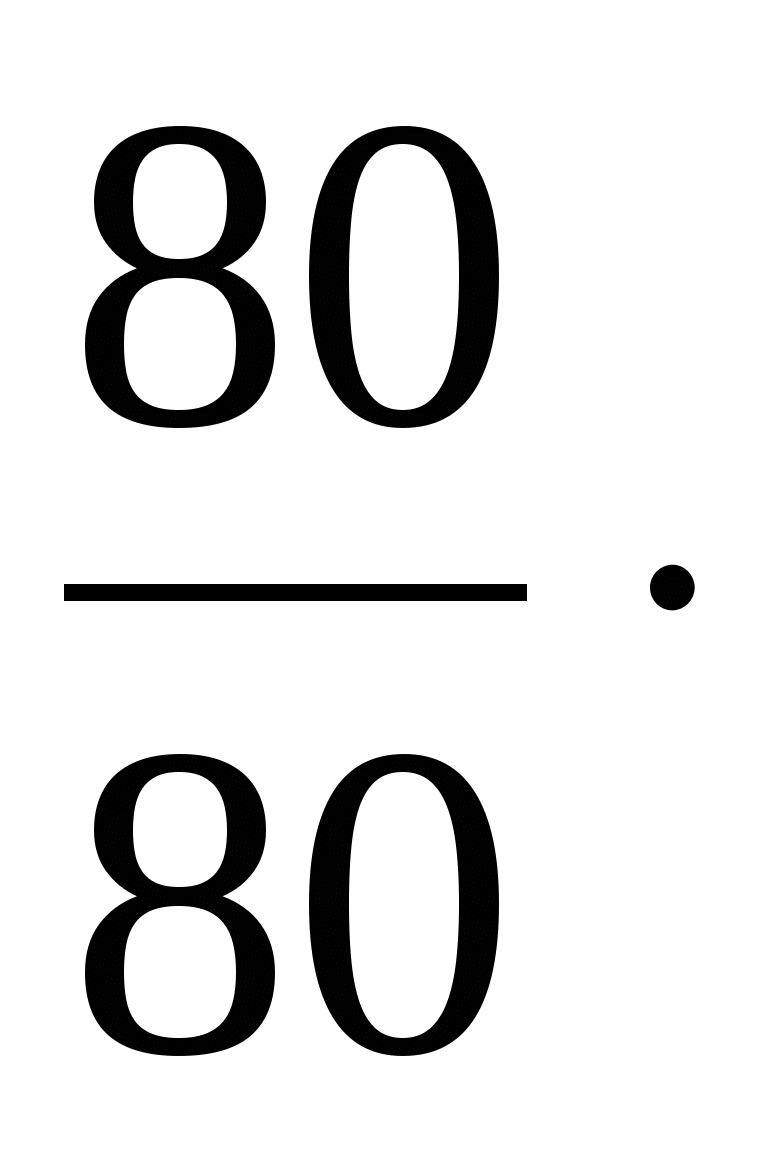 (ίv) n,
откуда (ίv) = .
Набор сменных колес для настройки гитары скорости резания: 31, 36, 41, 53, 59,64, 69, 47. Суммарное число зубьев гитары скорости резания (рисунок 5) должно быть равно Z∑ = 100.
Рисунок 5
3) Настройка направления.
Направление перемещения резцов обеспечивается кривошипно-шатунным механизмом. Кроме того, необходимо установить угол конусности зуба конического зубчатого колеса, значение которого выбирается из приложения Б (п. 28) в соответствии с вариантом задания. Обеспечивается этот угол установкой сегментов с суппортами резцов по шкале 6 (рисунок 6).
Рисунок 6
Для установки суппортов с резцами на угол конусности зуба необходимо отпустить гайки 4 (рисунок 6) и, поворачивая за квадрат 3, установить необходимый угол по шкале 6. После установки суппортов затянуть гайки. Установка угла каждого суппорта производится раздельно.
4) Настройка на путь.
Как было указано выше, рекомендуется задавать длину хода резцов на 8 мм больше ширины нарезаемого колеса. Для установки длины хода резцов необходимо открыть дверцу 1 передней бабки (рисунок 7), расцепить мелкомодульную муфту 2 (рисунок 8), на которой нанесены деления, соответствующие длине хода резцов, сцепить ее и затянуть гайкой 1.
5) Настройка исходного положения резцов.
Настройка исходного положения резцов производится по заготовке, поэтому, прежде всего, необходимо установить ее на оправку в шпиндель бабки изделия и закрепить с помощью гидравлического патрона. Далее поворотная плита 14 (рисунок 7) со шпиндельной бабкой 13 поворачивается относительно оси на угол конуса впадины ί нарезаемого колеса (раздел.4.3). Затем бабка изделия с помощью винта 2 смещается назад в осевом направлении и с помощью рычага 3 управления реверсивным золотником стол с бабкой изделия подводится до упора к передней бабке 4. Бабка изделия 13 перемещается в осевом направлении к резцам так, чтобы вершины резцов оказались на расстоянии 1– 1,5 мм от поверхности заготовки. Далее поворотом шпинделя за гайку 1 (рисунок 8) резцы устанавливаются в крайние положения. Для установки резцов относительно венца необходимо открепить гайки 1 (рисунок 6) и переместить резцедержки по Т - образному пазу суппортов так, чтобы обеспечить вход и выход резцов по длине зуба (врезание – 5 мм, перебег – 3 мм) и закрепить гайки 1.
Рисунок 7
Рисунок 8
(рисунок 7). Стол станка подводится с помощью гидроцилиндра 16, управляемого рукояткой 3. Центр станка является той точкой, которая совпадает с вершиной делительного конуса нарезаемого зубчатого колеса в процессе обработки (обката), а образующая конуса впадин совмещается при этом с центральной плоскостью. Установка резцов производится по приборам в следующей последовательности:
1 Установка угла профиля производится с помощью контрольной оправки 1 (рисунок 9), устанавливаемой в шпиндель бабки изделия 2, и контрольного резца 3. Регулировка производится с помощью клина 4 до совмещения режущей кромки резца с плоскостью а контрольной оправки. Эта установка производится на длительный период эксплуатации станка, поэтому ее выполнение в лабораторной работе не предусмотрено.
Рисунок 9
2 Установка резцов по высоте. Эта установка предусматривает совмещение вершин резцов с центральной плоскостью станка и производится по схеме (рисунок 10). Вначале прибор для установки резцов настраивается по индикатору на ноль на контрольном блоке (рисунок 10,а), затем устанавливается на резцедержатель (рисунок 10,б). Резец перемещается в резцедержке до тех пор, пока индикатор не покажет ноль. После зажима резца проверяют правильность установки. Эту операцию проделывают для обоих резцов.
Рисунок 10
Рисунок 11
3 Установка резцов по боковой режущей кромке. Данная установка резцов производится по аналогии с предыдущей по схемам представленным на рисунках 11,а и 11,б. Регулировка положения режущей кромки резца достигается с помощью винта 2 при ослабленном положении винта 1 (рисунок 6).
4.2 Кинематическая группа создающая движение обкатной подачи Фs (B2 B3)
Это движение сложное с незамкнутой траекторией (профиль одного зуба), поэтому необходимо настроить все пять параметров движения.
1) Настройка траектории (профиля зубьев). Внутренняя связь (рисунок 4).
УН I об. ППК → оборотов заготовки
∙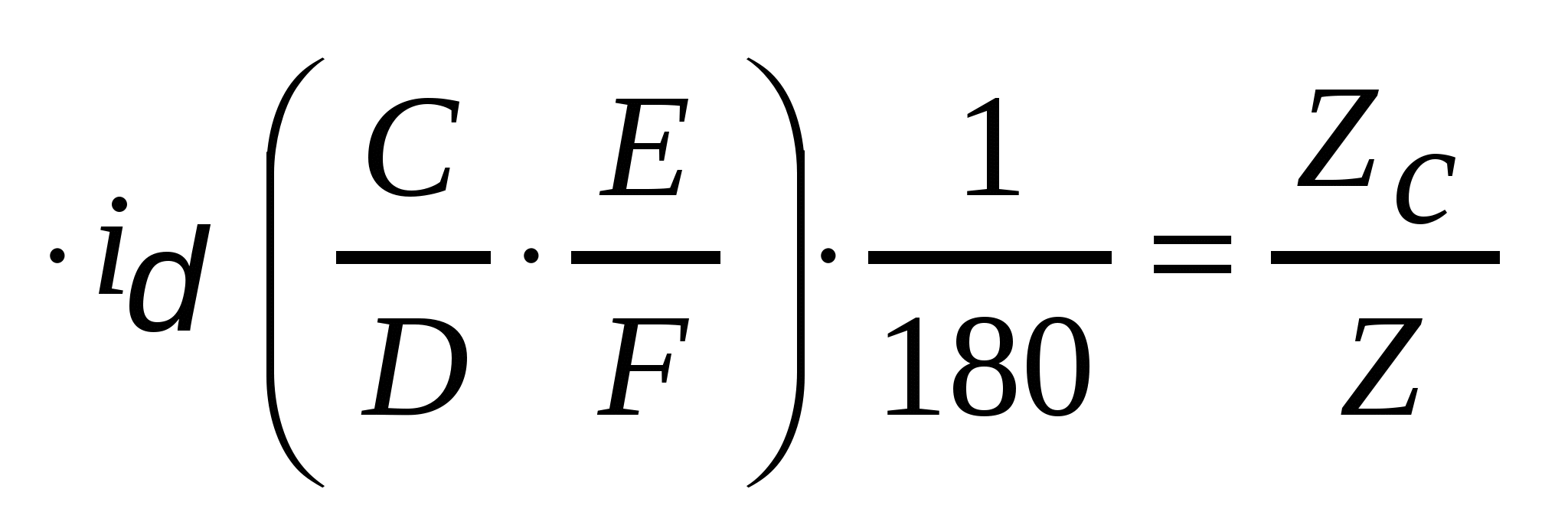 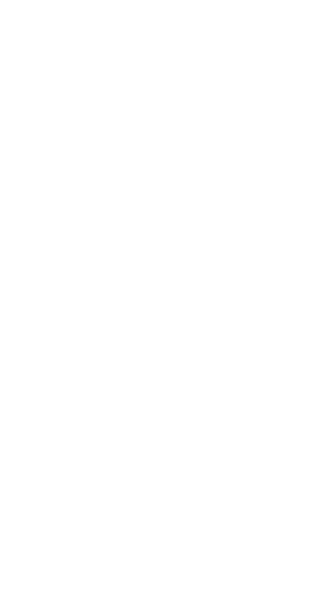 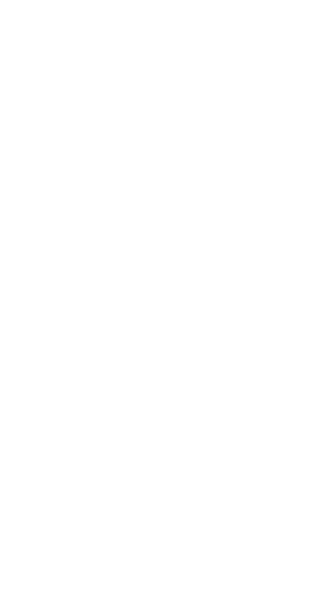
где ίх - передаточное отношение органа настройки цепи обката (рисунок 12);
Zc – число зубьев плоского производящего колеса;
Z - число зубьев нарезаемого зубчатого колеса;
ίd = - передаточное отношение органа настройки в цепи деления, полученное из уравнения кинематического баланса для цепи деления (раздел 4.3).
Подставляя вместо ίd его значение, и произведя соответствующие преобразования, в окончательном виде получим:
где Zί – число пропускаемых зубьев при делении (смотри движение деления).
Примечание расчеты передаточного отношения ίх произвести после выполнения расчетов по всем последующим разделам.
Полученное передаточное отношение обеспечивается подбором сменных колес по «Таблицам подбора сменных шестерен по передаточному отношению». Подбор осуществляется таким образом, чтобы значение ίx, полученное с точностью до пятого знака, обеспечивалось сменными зубчатыми колесами.
Рисунок 12 Сменные зубчатые колеса цепи обката
Сменные зубчатые колеса цепи обката находится под крышкой 5 (рисунок 7). При сцеплении шестерен гитары предусмотреть боковой зазор между зубьями 0,05 – 0,1мм. Сменные шестерни цепи обката и деления:
24 – 30 – 31 – 33 – 34 – 36 – 37 – 39
40 – 41 – 42 – 43 – 44 – 46 – 47 – 48
50 – 52 – 53 – 54 – 56 – 58 - 59 – 60
61 – 62 – 63 – 64 – 66 – 68 – 69 – 70
71 – 72 – 73 – 74 – 75 – 76 – 78 – 79
80 – 82 – 83 – 86 – 89 – 90 – 91 – 93
94 – 97 – 100 – 101 – 104 – 109 , всего 55 штук.
2) Настройка скорости обката (обкатной подачи).
Величина скорости обкатной подачи в станках рассматриваемого типа задается временем цикла в с, т.е.
tц = tр + tх,
где tр – время обката (рабочего хода), с;
tх – время холостого хода, с.
В связи с тем, что циклом работы управляет распределительный вал (РВ), то условие настройки может быть представлено следующим образом:
tр → часть оборота РВ,
где - угол поворота РВ за время рабочего хода, ( , из паспорта станка).
УКБ: tр =
где
Движение подачи заимствуется от электродвигателя постоянного тока М2 с тиристорным приводом. Двигатель имеет бесступенчатое регулирование частот вращения от 200 до 2000 об/мин, которое определяет рабочее время цикла и устанавливается с помощью рукоятки потенциометра по шкале расположенной на электрошкафу. Время рабочего хода и соответствующая ему частота вращения якоря электродвигателя выбирается по таблице 1.4. Меньшие значения tр выбираются для обработки зубчатых колес повышенной точности, большие значения tр – для зубчатых колес из материалов пониженной твердости и менее точных. Выбранная частота вращения электродвигателя измеряется тахометром.
Таблица 1.4
Время рабочего хода tр (с) по потенциометру
|
Показания тахометра nэ (об/мин) эл. двигателя подачи
|
Время
холостого хода tх (с)
|
Общее время цикла
tц (с)
|
53
|
200
|
5
|
58
|
43
|
250
|
5
|
48
|
35
|
300
|
5
|
40
|
30
|
355
|
4
|
34
|
25
|
425
|
4
|
29
|
20
|
535
|
4
|
24
|
15
|
710
|
3,5
|
18,5
|
12
|
900
|
3
|
15
|
10
|
1065
|
3
|
13
|
8
|
1330
|
3
|
11
|
6
|
1770
|
3
|
9
|
5
|
2000
|
3
|
8
|
3) Настройка направления обката.
В связи с тем, что ППК (механизм, воплощающий собой ППК) имеет только один зуб исходного контура производящей рейки, то для нарезания очередного зуба необходимо механизм (ППК) возвращать в исходное положение. С этой целью используется реверсивное устройство с составным подковообразным колесом.
С вала ХI (рисунок 4) вращение передается через зубчатые цилиндрические колеса Z = 61, 62, 61 ведущей шестерни Z = 20 реверсивного механизма, которая зацепляется то с наружным (Z = 120, прямой рабочий ход), то с внутренним венцом реверсивного колеса (Z = 80 – обратный, холостой ход), заставляя его вращаться то в одну, то в другую сторону. При этом через ведомое зубчатое колесо Z = 24, шестерни гитары обката (ίх) (рисунок 4) и червячную передачу осуществляется качание механизма ППК.
Реверсивное составное колесо состоит из двух участков: первый из них – целый, кольцеобразный, с наружным венцом Zн = 120 и внутренним Zв = 80. Второй участок – составной, подковообразный, зубья наружного и внутреннего венцов служат продолжением зубьев первого участка и соединяются между собой полушестернями, образуя подкову. Вал ХIII ведущей шестерни Z = 20 находится в рычаге, который может поворачиваться относительно оси вала ХII и перемещаться вдоль нее для осуществления необходимого зацепления с реверсивным колесом. Ведущая шестерня Z = 20 во время рабочего хода зацепляется с наружным венцом Zн = 120 реверсивного колеса и, после того, как ведомое колесо Z = 24 совершит пять полных оборотов, она перемещается вдоль зуба под действием кулачка К5 на валу VIII и переходит в зацепление с составным участком. Затем по полушестерне Z = 10 входит в зацепление с внутренним венцом Zв = 80 и, наконец, перемещаясь вдоль зуба, с его целым участком.
После того как ведомое колесо Z = 24 сделает 5 оборотов в обратную сторону (холостой ход) ведущая шестерня Z = 20 перемещается вдоль зуба на составной участок и по полушестерне
Z = 10 на его наружный венец Zn = 120. Затем шестерня Z = 20 перемещается вдоль зуба на наружный венец целого участка реверсивного составного колеса, и цикл начинается снова.
4) Настройка на путь (угол качания механизма ППК).
Угол качания (град.) рассчитывается по формуле:
ППК = arccos 0,5 ′ ,
где е – угол конуса выступов нарезаемого конического колеса, град.;
- угол конуса впадин нарезаемого колеса, град.;
' = .
Расчетное значение величины угла обката ППК обеспечивается кинематической цепью, связывающей элементарные движения ППК и заготовки.
5) Настройка исходного положения (установка угла механизма ППК).
Для установки исходного положения ППК необходимо открыть дверцу 6 (рисунок 7), и, вращая за квадрат червяка червячной пары распределительного вала, совместить риску ״середина обкатки״ на кольце под червячным колесом с неподвижно закрепленным указателем.
Далее открывают дверцу 5 (рисунок 7), гитары обката, снимают ведомую сменную шестерню (L) и ключом за вал червяка механизма ППК устанавливают последний так, чтобы его нулевая отметка совпадала с нулевой отметкой неподвижной шкалы 5 (рисунок 6). Это положение ППК соответствует середине обката. Затем сменную шестерню L ставят на место так, чтобы валы не провернулись на величину более чем необходимую для сцепления шестерен.
4.3 Кинематическая цепь, обеспечивающая движение деления Д (В4)
Во время холостого хода для возможности нарезания очередного зуба заготовке сообщается движение деления Д (В4). Причем, с целью исключения работы одного из резцов в уже обработанной впадине, делительный поворот заготовки производится на нарезание не соседнего зуба, а на определенное число пропускаемых зубьев Zi. Значение Zi рассчитывается по формуле:
где ППК - угол качания, град;
Zc – число зубьев плоского производящего колеса.
Полученное значение Zi округляется до ближайшего большего, причем так, чтобы это число не было кратно числу зубьев нарезаемого конического колеса и не имело с ним общих множителей.
В связи с тем, что делительный поворот происходит один раз за цикл, т.е. за один оборот распределительного вала, кинематическая цепь деления связывает распределительный вал и заготовку.
УН: I об. РВ → Zi / Z оборотов заготовки.
На рисунке 13 изображен эскиз расположения сменных зубчатых колес цепи деления. Для обеспечения возможности сцепляемости зубчатых колес, необходимо выдержать минимальную и максимальную суммы чисел зубьев сцепляемых колес, указанных на рисунке. Сменные зубчатые колеса берутся те же, что и для органа настройки в цепи обката. Орган настройки цепи деления расположен под крышкой 13 (рисунок 7).
Рисунок 13
4.4 Движение врезания
Под движением врезания на станке 5236П понимаются все установочные перемещения бабки изделия, обеспечивающие получение полной высоты зубьев нарезаемого колеса. К этим установочным перемещениям относятся:
осевая установка бабки изделия;
угловая установка бабки изделия;
установка стола;
установка двухпроходного механизма;
движение врезания, используемое при комбинированном способе нарезания конических колес.
Кратко остановимся на каждом из них.
1) Осевая установка бабки изделия
Осевой установкой называется расстояние Мс, мм, (рисунок 14) от центра станка до торца шпинделя I бабки изделия:
Мс = Ам + Б , где Ам – размер по чертежу детали 2 (согласно варианту задания);
Б ширина бурта оправки, (из таблицы вариантов заданий).
Рисунок 14
При посадке оправки в шпиндель бабки изделия от руки, зазор должен быть равен 0,05 0,1 мм, при затягивании оправки с помощью струны 4 зазор должен выбираться. Оправка снимается с помощью тяги гайки 5. Полученный размер устанавливается по шкале линейки и нониусу (рисунок 7), для чего отпускаются гайки 8 и с помощью винта 2 перемещается бабка изделия в осевом направлении.
2) Угловая установка бабки изделия
Здесь преследуется цель совместить образующую конуса впадин обрабатываемого зубчатого колеса с центральной плоскостью (плоскостью, в которой перемещаются вершины резцов, рисунок 7). Для установки бабки изделия на угол внутреннего конуса нарезаемой шестерни, необходимо освободить гайки 9 поворотной плиты и повернуть бабку изделия на угол по шкале 11 и нониусу 12 с точностью до 15 с. После перемещения снова закрепить гайки поворотной плиты.
3) Установка стола
Стол устанавливается относительно резцов так, чтобы вертикальная ось поворотной плиты проходила через центральную плоскость, в которой лежат вершины резцов.
Вследствие того, что вся настройка задается по плоскому производящему колесу, образующая внутреннего конуса заготовки должна лежать в центральной плоскости станка.
Положение стола относительно резцов определяется установкой нониуса 1 (рисунок 15). При совпадении оси поворотной плиты с центральной плоскостью станка нониус показывает ноль, (регулировка производится винтом 4).
Рисунок 15
4) Установка двухпроходного механизма
Обычно обработку на станке ведут в два прохода (черновая и чистовая обработка), для чего устанавливают маховик 3 (рисунок 15) на величину требуемого припуска, оставляемого на второй проход.
При чистовом нарезании шестерни маховичок двухпроходного механизма устанавливается в нулевое положение.
Двухпроходный механизм представляет собой валик 2 (рисунок 15), на котором имеются площадки разной высоты. В зависимости от величины припуска соответствующая площадка упирается в жесткий упор 5 станины. На маховике 3 нанесены деления, указывающие величину припуска на второй проход 0,05; 0,15; 1,5; 2,5 мм.
5) Движение врезания, используемое при комбинированном способе нарезания конических колес.
При нарезании колес с углом начального конуса 700 и больше необходимо иметь угол качания механизма ППК больше 700, что не рекомендуется для работы станка. Поэтому нарезание таких колес ведут комбинированным способом, при котором одновременно с обкаткой происходит врезание инструмента в заготовку. Это осуществляется за счет особого кулачка К2 (рисунок 4), сидящего на распределительном валу. Когда инструмент врежется в заготовку до предельного положения, врезание прекращается и происходит формирование профиля методом обката.
При комбинированном способе нарезания необходимо сделать дополнительный расчет и дополнительную наладку станка, что не входит в задачи лабораторной работы.
4.5 Вспомогательные движения и движения управления (рабочий цикл станка)
После нарезания очередного зуба с помощью кулачка К1 распределительного вала (рисунок 4) бабка изделия отводится от центральной плоскости на 8 мм. В конце отвода с помощью кулачка К3 срабатывает конечный выключатель, который исключает потенциометр управления из электрической цепи питания двигателя постоянного тока, в результате чего поворот механизма ППК в исходное положение и делительный поворот заготовки на число пропускаемых зубьев происходит ускоренно (холостой ход). В конце холостого хода подключается потенциометр управления двигателем, механизм ППК начинает вращаться в другую сторону, бабка изделия с помощью кулачка К1 выводится в исходное положение и начинается рабочий ход. В конце его бабка изделия отводится и цикл повторяется. За I оборот распределительного вала совершается цикл работы станка, т.е. нарезается один зуб. Следовательно, для нарезания зубчатого колеса с числом зубьев Z необходимо совершить Z циклов. Счет циклов производится по диску 10 (рисунок 7), управляемого кулачком К4 распределительного вала.
Станок модели 5236П гидрофицирован. Гидравлика используется для зажима детали, подвода и отвода стола с бабкой изделия на расстояние до 100 мм, для подвода диска счетчика циклов, смазки узлов и механизмов станка и для охлаждения. Отработанное масло очищается рядом фильтров и сливается в бак.
5 Циклограмма работы станка
Последовательность элементов цикла и их длительность, определяющих время цикла (время обработки одного зуба), можно представить в виде циклограммы (рисунок 16). Согласно приведенному примеру циклограммы время цикла составило около
22 с, время обработки одной детали – около 626 с. В лабораторной работе необходимо с помощью секундомера измерить время элементов цикла для выполненной настройки наладки станка и построить циклограмму по упрощенной схеме (без наименования узлов команд по рисунку 16).
Таблица 2 – Циклограмма работы станка
Рисунок 16
6 Варианты задания
1
|
2
|
3
|
4
|
Параметры конической зубчатой передачи
|
∑ = 900
|
∑ = 900
|
∑ = 900
|
∑ = 900
|
|
|
|
|
α = 200
|
α = 200
|
α= 200
|
α = 200
|
m = 1,75
|
m = 1,75
|
m = 1,75
|
m = 1,75
|
Степень точности
8-7-7Вв
|
Степень точности
7Вв
|
Степень точности
8-8-7Аа
|
Степень точности
7-6-6-Сс
|
Материал
сталь 45
|
Материал
сталь 45
|
Материал
сталь 45
|
Материал
сталь 45
|
Размер Б оправки
|
49,4
|
49,4
|
49,4
|
49,4
|
Нарезание зубьев на станке
|
1
|
2
|
1
|
2
|
1
|
2
|
1
|
2
|
|
Zш
|
Zk
|
Zш
|
Zк
|
Zш
|
Zк
|
Zш
|
Zк
|
|
Примечание Расшифровка обозначений параметров приведена в приложении Б.
7 Меры безопасности
7.1 Практическую часть работы разрешается выполнять только после изучения теоретической части лабораторной работы.
7.2 Запрещается включать станок без разрешения учебного мастера или преподавателя.
7.3 Настройку и наладку производить только исправным инструментом.
8 Содержание отчета
8.1 Цель лабораторной работы.
8.2 Задание: эскиз детали согласно варианту, таблица основных параметров, численные значения всех остальных параметров (приложение Б и В).
8.3 Структурная схема станка (рисунок 3).
8.4 Анализ кинематической группы создающей движение скорости резания Фv(П1):
8.4.1 Расчеты по настройке скорости резания, рисунок органа настройки.
8.4.2 Краткие пояснения по настройке направления.
8.4.3 Краткие пояснения по настройке на путь и исходное положение.
8.5 Анализ кинематической группы создающей движение обкатной подачи Фs(В2В3).
8.5.1 Расчеты по настройке траектории (условие настройки, уравнение кинематического баланса, формула настройки, расчет передаточного отношения и подбор сменных колес в цепи обката).
8.5.2 Расчеты по настройке скорости обката.
8.5.3. Краткое пояснение по направлению обката (за счёт чего достигается).
8.5.4 Расчет угла качания механизма ППК.
8.5.5 Краткое пояснение по настройке исходного положения.
8.6 Анализ кинематической группы, обеспечивающей движение деления Д(В4).
8.6.1 Расчет числа пропускаемых зубьев.
8.6.2 Расчет передаточного отношения органа настройки и подбор сменных колес.
8.7 Анализ движения врезания ВР (П5).
8.7.1 Рисунок 14 и расчеты по осевой установке бабки изделия.
8.7.2 Краткие пояснения по угловой установке бабки изделия.
8.8 Циклограмма работы.
Контрольные вопросы
1 Назовите основные параметры конической передачи и конического зубчатого колеса.
2 Что представляет собой плоское производящее колесо (ППК)?
3 Чему равно число зубьев ППК?
4 Какими методами и какими формообразующими движениями получаются образующая (прямая) и направляющая (профиль зубьев) производящие линии конического зубчатого колеса?
5 Какова структура формообразующей части станка и почему?
6 Назовите условие настройки на скорость резания.
7 Что понимается под центральной плоскостью и центром станка?
8 Назовите порядок настройки исходного положения резцов.
9 Назовите условие настройки станка на получение заданного профиля зубьев конического колеса.
10 Назовите условие настройки станка на получение заданной скорости обкатной подачи.
11 Составьте уравнение кинематического баланса с целью определения передаточного отношения органа настройки в цепи, определяющей получение профиля зубьев.
12 Составьте уравнение кинематического баланса для цепи, определяющей скорость обката.
13 Назовите условие настройки для цепи деления.
14 Составьте уравнение кинематического баланса для цепи деления.
15 Поясните циклограмму работы зубострогального полуавтомата.
Литература
1 Проников А.С., ред. Металлорежущие станки и автоматы. М.: Машиностроение, 1981. 530 с.
2 Пуш В.Э. Конструирование металлорежущих станков. М. : Машиностроение, 1986. 495 с.
3 Федотенок А.А. Кинематическая структура металлорежущих станков. М. : Машиностроение, 1970. 490 с.
4 Маеров А.Г. Устройство, основы конструирования и расчет металлорежущих станков и автоматических линий. М. : Машиностроение, 1986. 367 с.
5 Колев Н.С. Красниченко Л.В. и др. Металлорежущие станки. М. : Машиностроение, 1980. 500 с.
Приложение А
(справочное)
Приложение Б
(справочное)
Расчетная карта А1 параметров шестерни и колеса
№
п/п
|
Параметры прямозубых
конических колес
|
Обозначение и расчетная формула
|
Варианты
|
11
|
2
|
3
|
4
|
1
|
Число зубьев шестерни
|
Zш
|
25
|
25
|
28
|
24
|
2
|
Число зубьев колеса
|
Zk
|
50
|
30
|
40
|
35
|
3
|
Передаточное отношение
|
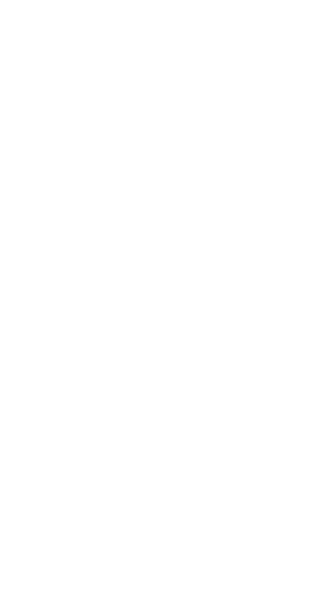
|
2
|
1,2
|
1,42857
|
1,45833
|
4
|
Коэффициент высотной коррек-ции (из справоч-ника)
|
|
0,29
|
0,1
|
0,19
|
0,166
|
5
|
Коэффициент радиального зазора
|
Кс
|
0,2
|
0,2
|
0,2
|
0,2
|
6
|
Число зубьев плоского колеса
|
Zc=
|
55,9017
|
39,051248
|
48,82622
|
42,43819
|
7
|
|
Сs=1,571+0,728
|
1,78212
|
1,6438
|
1,70932
|
1,6918
|
8
|
Модуль
|
M
|
1,5
|
1,75
|
1,75
|
1,75
|
9
|
Длина образующей начального конуса
|
Le = 0,5 mZc
|
41,26
|
34,1698
|
42,72294
|
37,133
|
10
|
Ширина зубчатого венца
|
B ≤ 0,3 Le
|
12
|
10
|
12
|
11
|
11
|
Глубина захода
|
h = 2m
|
3
|
3,5
|
3,5
|
3,5
|
12
|
Радиальный зазор
|
С = Кс ∙ m
|
0,3
|
0,35
|
0,35
|
0,35
|
13
|
Полная высота зуба
|
h = h + C
|
3,3
|
3,85
|
3,85
|
3,85
|
14
|
Окружной шаг
|
t = 3,1416 m
|
4,7124
|
5,49799
|
5,497787
|
5,497787
|
15
|
Диаметр начальной окружности
|
Dш= Zш ∙ m
|
37,5
|
43,75
|
49
|
42
|
16
|
Высота головки зуба
|
Hгш = m(1+ )
|
1,935
|
1,925
|
2,0,8
|
2,04
|
17
|
Высота ножки зуба
|
hнш = h – hгш
|
1,365
|
1,925
|
1,77
|
1,809
|
18
|
Угол начального конуса
|
ш = аrctg
|
26034′
|
39048′20״
|
350
|
34026′20״
|
19
|
Тригонометрические функции угла начального конуса
|
Sin ш
Cos ш
|
0,447214
0,894427
|
0,640184
0,768222
|
0,573462
0,319232
|
0,565528
0,824729
|
20
|
Угол ножки зуба
|
ш = arctg
|
1051′53״
|
3013′26״
|
2022′
|
2047′73״
|
Продолжение приложения Б
(справочное)
Расчетная карта параметров шестерни
21
|
Угол наружного конуса
|
|
29037′5״
|
43036′53״
|
38015′32״
|
3807′
|
22
|
Угол внутреннего конуса
|
|
24042′
|
36034′52״
|
32038′
|
31038′57״
|
23
|
Наружный диаметр
|
cos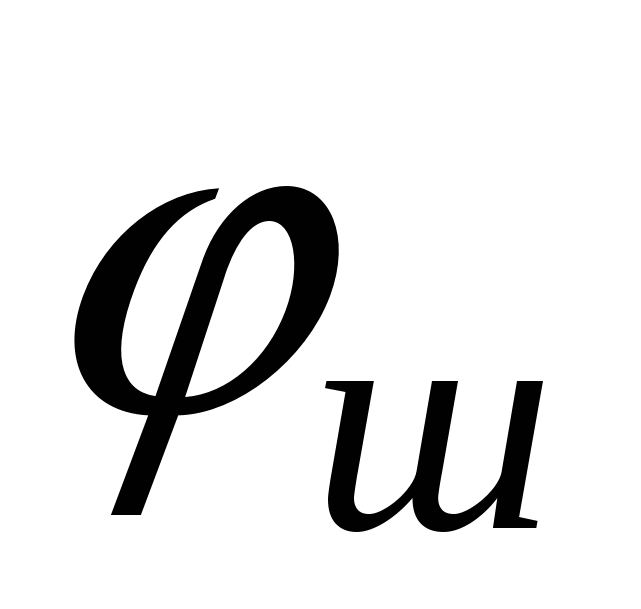
|
40,96
|
46,71
|
52,412
|
45,37
|
24
|
Расстояние вершины начального конуса от базового торца
|
Аш - конструктивно
|
44,0
|
37
|
44
|
40
|
25
|
Расстояние базового торца от зубчатого венца
|
А =А-Le∙ cos φш +
+ hгш ∙ sin φш
|
7,93
|
11,98
|
10,19
|
10,53
|
26
|
Ширина ступицы
|
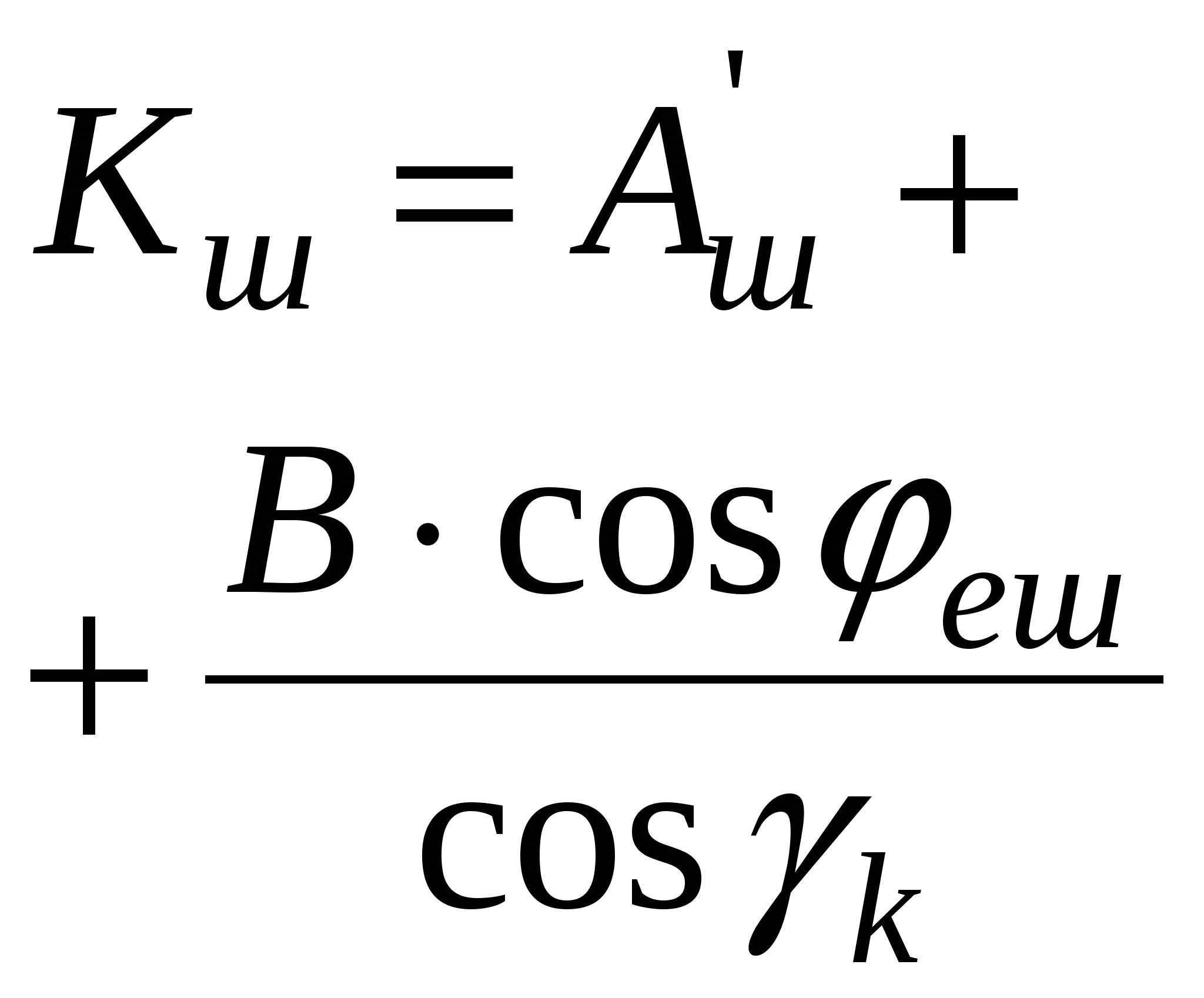
|
18,43
|
19,24
|
19,63
|
19,20
|
27
|
Толщина зуба по дуге начальной окружности
|
Sш =
|
2,67318
|
2,88
|
2,99
|
2,96
|
28
|
Угол конусности зуба в градусах
|
∙cosγш
|
2030′20״
|
3035′13״
|
2052′
|
3018׳2״
|
29
|
Угол толщины зуба
|
|
0,063759
|
0,05051
|
0,050
|
0,058138
|
30
|
Коэффициент в зависимости от W
|
K′wш = 0,99929
К״wш = 0,01625
|
|
0,99957
|
0,99958
|
0,99944
|
31
|
Измерительная толщина зуба
|
Sш״ = Sш∙К′шw=Sx
|
2,67
|
2,88
|
2,99
|
2,96
|
32
|
Измерительная высота зуба
|
hгш ״∙hгш+Sш∙Кwш״=
= hx
|
1,978439
|
1,96168
|
2,12
|
2,083
|
Продолжение приложения Б
Расчетная карта параметров колеса
Расчетная карта А1 (продолжение)
№
п/п
|
Обозначение параметров и расчетные
формулы для колеса
|
Варианты
|
1
|
2
|
3
|
4
|
15
|
Dк = Zк ∙ m
|
75
|
52,5
|
70
|
61,25
|
16
|
hгк = h3 – hгш
|
1,065
|
1,575
|
1,42
|
1,4595
|
17
|
hHK =h – hгк
|
2,235
|
2,275
|
2,43
|
2,3905
|
18
|
|
63026׳6״
|
50011׳40״
|
550
|
55033׳40״
|
19
|
сosφк
sin φк
|
0,447214
0,894427
|
0,640184
0,768222
|
0,573462
0,81923
|
0,565528
0,824729
|
20
|
|
3035״
|
3048׳33״
|
3015׳32״
|
3041׳20״
|
21
|
|
65018׳
|
53025׳8״
|
57022״
|
58021׳
|
22
|
|
60023׳
|
46021׳6״
|
51044׳24״
|
51052׳40״
|
23
|
Dек = dк+2hгк соsφк
|
75,953
|
54,516
|
71,63
|
62,90
|
24
|
AK(конструктивно)
|
|
|
|
|
25
|
А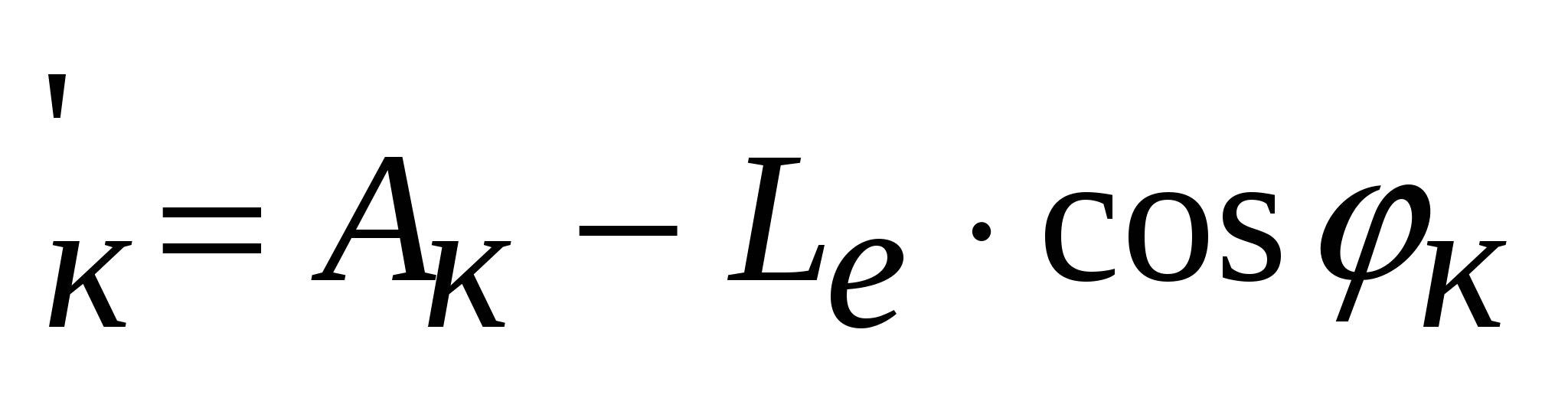
|
|
|
|
|
26
|
Kк=
|
|
|
|
|
27
|
Sк = t – Sш
|
2,03922
|
2,62114
|
2,51
|
2,54
|
28
|
|
2030׳20״
|
3035׳10״
|
2052׳
|
3018׳
|
29
|
Wк =
|
0,0121595
|
0,03196
|
0,02053
|
0,023425
|
30
|
= 0,99995
|
|
0,99983
0,00806
|
0,99990
0,005
|
0,99989
0,00575
|
31
|
|
2,039118
|
2,62
|
2,51
|
2,537
|
32
|
|
1,0711176
|
1,60
|
1,43
|
1,474088
|
Приложение В
(справочное)
Рабочий чертеж зубчатого колеса к варианту 1
Вариант 1
Продолжение приложения В
Рабочий чертеж зубчатого колеса к варианту 2
-
Вариант 2
Продолжение приложения В
Рабочий чертеж зубчатого колеса к варианту 3
-
Вариант 3
Продолжение приложения В
Рабочий чертеж зубчатого колеса к варианту 4
-
Вариант 4
Содержание
Введение ................................................................................. 3
1 Цель и задачи лабораторной работы .................................. 4
1.1 Цель лабораторной работы ....................................................4
1.2 Задачи лабораторной работы .................................................4
2 Назначение и техническая характеристика
зубострогального полуавтомата мод. 5236П .......................4
3 Принцип нарезания зубьев на
зубострогальных полуавтоматах типа 5236П ..................... 5
4 Расчет параметров, настройка и наладка станка .................9
4.1 Кинематическая группа, создающая движение
скорости резания Фv(П1) ........................................................9
4.2 Кинематическая группа, создающая движение
обкатной подачи Фs(В2 В3) ...................................................19
4.3 Кинематическая цепь, обеспечивающая движение
деления Д (В4) ........................................................................24
4.4 Движение врезания ...............................................................25
4.5 Вспомогательные движения и движения управления
(рабочий цикл станка) ..........................................................28
5 Циклограмма работы станка ................................................29
6 Варианты задания ................................................................ .31
7 Меры безопасности ...............................................................31
8 Содержание отчета ............................................................. ..31
Контрольные вопросы ..........................................................33
Литература .............................................................................34
Приложение А........................................................................35
Приложение Б ........................................................................36
Приложение В .......................................................................39
страница 1
|