страница 1 ... страница 5 | страница 6 | страница 7 страница 8
Средства диагностирования гидропривода термодинамическим методом. На рисунке 51 показана схема включения средств измерения для диагностирования гидронасосов термодинамическим методом. Для измерения средней температуры рабочей жидкости во всасывающей магистрали установлен термистор 3, включенный в мостовую измерительную схему 2 со стрелочным прибором 1.
Рисунок 51 - Схема включения измерительных средств при диагностировании насоса термодинамическим методом
Ультразвуковой течеискатель состоит из ультразвукового щупа и блока приборов. В корпусе 1 щупа (рисунок 52, а) установлен контактный акустический волновод 2, который плотно прижимают к ОД с помощью пружины 4. На дне волновода размещен пьезоэлектрический ультразвуковой преобразователь 3. В рукоятку щупа встроен согласующий усилитель 5. Щуп соединен с блоком приборов гибким кабелем. Сигнал с выхода согласующего усилителя поступает на переключатель диапазонов измерения, далее на вход усилителя 8. После усиления сигнал детектируется детектором 9 и интегрируется интегратором 10.
Время интегрирования сигнала может быть изменено в необходимых пределах с помощью блока управления временем интегрирования 13 и коммутатора 12.
Градуировка блока приборов осуществляется от генератора шума 6 через специальный атенюатор 7. Уровень шума отсчитывают по стрелочному прибору 11, проградуированному в микровольтах и децибеллах.
а – ультразвуковой щуп;
б – блок приборов
Рисунок 52 – Ультразвуковой течеискатель
Приборы для анализа состояния рабочих жидкостей в гидравлических системах ОД. Прибор для определения объемной концентрации загрязнений рабочих жидкостей. Этот прибор основан на нефелометрическом методе, т. е, на сравнении интенсивности двух световых потоков: рассеянного эталонной жидкостью, т. е. жидкостью того же типа, что и анализируемая, но не содержащей загрязнений, и рассеянного жидкостью, содержащей частицы загрязнении.
Рисунок 53 - Схема прибора для определения концентрации загрязнении рабочих жидкостей
Прибор для определения гранулометрического состава загрязнений в пробах жидкости. Прибор СМЧ-1 основан на оптическом сканировании плоской пробы жидкости или сканировании осветленного фильтра после пропускания через последний пробы загрязненной жидкости определенного объема. Схема прибора показана на рисунке 54. На столике 3 прибора размещают контейнер 4 с пробой жидкости толщиной не более 60 мкм или осветленный фильтр. Световой поток от источника света 1 проходит через конденсатор черного поля 2 и пробу жидкости и стекло 5 попадает на окуляр микроскопа 6. Далее через призму 7 и щелевую диафрагму 8 попадает на фотокатод ФЭУ 9.
Столик с пробой с помощью механического развертывающего устройства 13 совершает возвратно поступательное движение с боковым смещением при каждом шаге. Размеры анализируемой прибором пробы 5x30 мм. При прохождении частицы в поле зрения микроскопа на выходе ФЭУ образуется импульс, амплитуда которого пропорциональна размеру частицы, затемняющей поле зрения микроскопа.
Выход ФЭУ через согласующий линейный усилитель 10 соединен с пятиканальным дифференциальным амплитудным дискриминатором И.
Каждый канал амплитудного дискриминатора (нижние и верхние пороги дискриминации) настроен так, что при анализе пробы осуществляется автоматический подсчет частиц по пяти размерным группам в соответствии с ГОСТ 17216—71:
Канал 1 2 3 4 5
Размеры частиц, мкм 5...10 10...25 25...50 50...100 Более 100
Результаты анализа выдаются на пяти цифровых электромеханических счетчиках 12. Известны приборы подобного назначения, в которых сканирование пробы осуществляется с помощью телевизионного видикона, например прибор «Миллипор» ПМС фирмы Джойс Лобель (США).
Рисунок 54 – Схема прибора для определения гранулометрического состава загрязнении в пробах жидкости
Приборы для классификации взвешенных частиц в рабочей жидкости. Действие приборов основано на определении с помощью фотоэлектрического преобразователя числа и размеров частиц, проходящих вместе с жидкостью через калиброванную щель.
Схема, поясняющая принцип действия преобразователя прибора фирмы ХАЕГ (США), показана на рисунке 55. Анализируемая жидкость из пробоотборника или непосредственно из диагностируемой гидравлической системы поступает под давлением в измерительный канал 1 и проходит через калиброванную щель 3 (размером 2,5 мм х 150 мкм), которая имеет по бокам прозрачные окна 4. С одной стороны щели установлена миниатюрная лампа 5, а с другой – фотодиод 6. При проходе каждой загрязняющей частицы 2 происходит частичное затемнение фотодиода, в результате на сопротивлении нагрузки фотодиода образуется импульс, амплитуда которого пропорциональна площади поперечного сечения частицы.
После усиления импульсы поступают на вход пятиканального амплитудного анализатора. Установленные на выходе анализатора электромеханические счетчики осуществляют регистрацию поступающих импульсов в соответствии с их амплитудами, а следовательно, с размерами частиц.
Прибор ХАЕГ имеет ту же ширину и число каналов анализатора, что и прибор СМЧ-1.
Предельная скорость счета на этом анализаторе 4000 частиц/с. Расход жидкости через преобразователь около 50 см3/мин, емкость пробоотборника 500 см3.
Для измерения количества жидкости, подвергаемой анализу в приборе имеется расходомер. Среднее время анализа с получением представительных результатов около 1 мин. Главное преимущество прибора ХАЕГ -возможность его применения не только для анализа проб, но и для непрерывного анализа при подключении прибора непосредственно в работающую гидросистему ОД.
а – измерительный канал;
б – увеличенный продольный разрез калиброванной щели
Рисунок 55 – Фотоэлектрический преобразователь прибора для определения гранулометрического состава загрязнения в потоке рабочей жидкости
Практическая работа №7 Средства диагностирования механических передач машин
Цель работы: Изучение содержания методов диагностирования и конструкции средств диагностирования механических передач машин.
Задачи работы: Научить студентов планировать и осуществлять диагностирование механических передач машин.
После выполнения работы студент должен
Знать: сущность рассмотренных методов диагностирования механических передач машин, области применения данных методов.
Уметь: назначать соответствующие методы и средства диагностирования применительно к диагностируемым параметрам механических передач машин.
При эксплуатации первых машин уже проводили периодическое их «вслушивание». Для локализации источников звукообразования использовали стетоскопы. С появлением виброметров объем получаемой информации увеличился за счет расширения частотного диапазона измерений и повышения точности оценки уровней. Многие современные средства диагностирования механических передач также основаны на виброаккустических методах.
7.1 Диагностические параметры и методы диагностирования
Суммарный угловой зазор. Суммарный угловой зазор механической передачи складывается из угловых зазоров ее составных частей. Например, суммарный угловой зазор трансмиссии автомобиля образуется суммарным угловым зазором коробки передач, суммарным зазором карданного вала и зазором в зубчатых передачах заднего моста. В свою очередь, суммарный угловой зазор в карданном вале является суммой зазоров: в шлицевом соединении, между шипами крестовины, игольчатыми подшипниками и отверстиями в вилках. Суммарный угловой зазор коробки передач складывается из боковых зазоров отдельных шестерен. Таким образом, изменение зазора в каждом сопряжении трансмиссии приводит к изменению суммарного углового зазора.
На рисунке 56 показаны кривые изменения суммарных угловых зазоров главных передач грузовых автомобилей ЗИЛ (кривая 1) и ГАЗ (кривая 2) в функции наработки (пробега). Эти кривые согласуются с общим законом изменения износа в функции наработки, т. е. за приработкой следует период износа со сравнительно малой постоянной интенсивностью, соответствующей периоду нормальной эксплуатации, переходящему затем в период прогрессирующего износа. Этот период характеризуется увеличенной интенсивностью нарастания угловых зазоров в 6...12 раз. Допустимые и предельные значения суммарных угловых зазоров нормированы для целого ряда механических передач. В частности, предельные значения для составных частей трансмиссий автомобиля следующие: коробка передач 5... 15°, карданная передача 5...6°, главная передача 55...65°.
Дифференцированные значения угловых зазоров. Один из методов определения дифференцированных значений угловых зазоров в закрытых передачах заключается в анализе кривых изменения момента сопротивления на входном или выходном валах передачи в процессе выбора предварительно накопленных зазоров. По кривым изменения момента в функции угла поворота можно судить о состоянии каждого элемента передачи.
Рисунок 56 – Кривые изменения суммарных угловых зазоров в функции наработки главных передач автомобилей
На рисунке 57, а показана схема зубчатой передачи, а на рис. 57, б – кривая изменения момента сопротивления на выходном валу передачи. Длины ступенек 1-4 соответствуют величинам зазоров в парах передачи (зубчатых 1, 2 и шлицевых 3, 4), а ординаты – величинам моментов, требуемых для выбора этих зазоров. Величины моментов характеризуют КПД сопряжений, в частности, по величинам этих ординат можно судить о регулировках подшипников и о состоянии смазки.
Регистрацию момента сопротивления осуществляют в функции угла поворота вала диагностируемого редуктора. Для получения информации об износе сопряжений по контуру, регистрацию кривых момента сопротивления производят многократно при различных начальных положениях вала ОД.
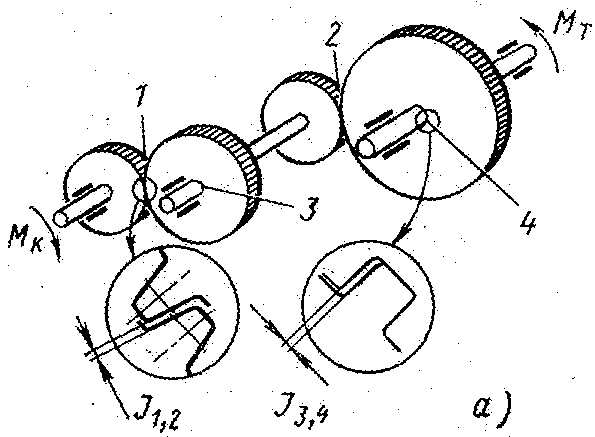
а-схема передачи;
б-зависимость момента сопротивления от угла поворота
Рисунок 57 – Определение момента сопротивления Мс для диагностирования двухступенчатой зубчатой передачи
Техническое состояние зацепления прямозубой цилиндрической передачи может быть охарактеризовано соотношением сил (рисунок 58): нормальной (N), окружной (Р), радиальной (R) и трения (F). Последняя направлена из полюса зацепления по касательной к профилям сопряженных зубьев. Сила N направлена нормально к касательной, поэтому искажение профилей вызывает изменение соотношений между силами R и Р. Угол наклона вектора W, характеризующего силы, может быть определен из выражения
α ρ= arctg (R/P) (7.1)
где α – угол между направлением нормали к профилям и направлением окружной силы Р;
ρ – угол, характеризующий коэффициент трения.
Угол а может быть определен по формуле
α = arctg[l/f’(x)] (7.2)
где f’ (х) – первая производная кривой, образующей профиль зуба.
Поскольку угол р в процессе эксплуатации меняется незначительно, обычно в сторону уменьшения (при номинальном значении 2...5° для передач, расположенных в масляной ванне), то, измеряя силы R и Р, можно определить величину угла а, который при предельных износах достигает величины 32...35°. На рисунке 59 показана зависимость величины угла а от износа зубьев по толщине для шестерен коробки передач трелевочного трактора ТДТ-75.
Рисунок 58 – Соотношения сил, действующих в зубчатом зацеплении
1,2-ведущая и ведомая шестерни
Рисунок 59 – Зависимость угла от износа зубьев в передаче
Изменения температуры. При создании постоянных нагрузок и скоростных режимов техническое состояние механических передач могут характеризовать закономерности изменения температуры. На рисунке 60 показаны кривые изменения температуры корпуса редуктора заднего моста автомобиля. На кривых можно выделить три временных фаз, соответствующих неупорядоченному нагреву А, регулярному тепловому режиму В И выходу на стационарный тепловой режим С.
Фаза неупорядоченного нагрева имеет случайный характер, ее не используют для получения информации о техническом состоянии, Стационарный режим, при котором достигается тепловое равновесие, неудобен, так как выход ОД на этот режим требует значительного времени. В связи с этим информацию получают во второй фазе нагрева, когда температура ОД меняется по экспоненциальному закону.
Интенсивность нарастания температуры (кривая 3) у неисправного редуктора будет выше допустимой (кривая 2), а у исправного ниже (кривая 1). Для получения информации об интенсивности нарастания температуры достаточно произвести два последовательных измерения: на начальном участке фазы регулярного теплового режима и спустя некоторое время. В начале фазы регулярного теплового режима экспоненциальная зависимость может быть аппроксимирована линейной, поэтому интенсивность нагрева на рассматриваемом участке может быть выражена тангенсом угла наклона кривой к оси абсцисс.
1-исправный редуктор;
2-граница допустимых значении;
3-неисправный редуктор
Рисунок 60 – Изменение температуры корпуса редуктора заднего моста автомобиля от времени
Более точные результаты диагностирования могут быть получены, если осуществлять регистрацию, например, с помощью самописцев, кривых изменения температуры или проводить ряд отдельных измерений через определенные интервалы времени с целью последующего анализа кривой изменения температуры. Если такие измерения нарастания температур проводить в нескольких заранее выбранных точках корпуса ОД и затем кривые изменения температуры сравнивать с эталонными, полученными на ОД без дефектов, то можно найти связи деформаций кривых с некоторыми видами локальных неисправностей.
Анализ масел. Одним из методов определения технического состояния зубчатых передач является определение весовой или объемной концентрации и скорости накопления в смазочных маслах продуктов износа деталей ОД. При постоянном количестве Q масла в передаче и при условии равномерного распределения продуктов износа в объеме масла интенсивность изменения концентрации продуктов износа Ук связана с интенсивностью износа Уи деталей ОД следующим соотношением:
Vк=Vи(Q + Kt)t (7.3)
где К — коэффициент интенсивности осаждения продуктов износа;
t — время между взятием анализов проб.
Электрическое сопротивление. При работе исправных механизмов масляный слой в трущихся парах подшипников обладает высоким активным сопротивлением. В трущихся парах, имеющих дефекты, сопротивление масляного слоя резко падает, в отдельных случаях практически до нуля. Этот эффект используют для определения технического состояния зубчатых передач и прогнозирования отказов на ранней стадии их возникновения.
Переходное сопротивление в трущихся парах зависит от частоты вращения, от нагрузок, приложенных к этим парам и от наличия в масле проводящих продуктов износа. Поэтому рассматриваемый диагностический параметр является интегральным. Для локализации неисправности по величине сопротивления необходимо иметь данные о режиме работы пары во время диагностирования (частота вращения, нагрузки) и информацию о наличии в масле проводящих продуктов. На рисунке 61 показана зависимость изменения переходного сопротивления шарикоподшипника № 204 от частоты вращения при радиальной нагрузке на вал 750 Н и осевой нагрузке 330 Н. Кривые 1 и 2 имеют инверсию при частотах вращения в диапазоне 3500—4000 об/мин, что требует выдерживания скоростного режима во время диагностирования. Влияние изменения осевой и радиальной нагрузок на относительное изменение сопротивления показано на рисунке 62. Виброакустические параметры. Уровень и спектр акустического шума. Шум, генерируемый механизмами, является следствием взаимодействия их деталей, в частности, в результате соударений, неуравновешенности, неровностей поверхностей качения и др. Уровень шума в широкой полосе частот – интегральный диагностический параметр. Повышение уровня шума может свидетельствовать о наличии какой-либо неисправности. Очень часто повышение уровня шума вызывают второстепенные неисправности, например, слабая затяжка крепления кожухов, вместе с тем шум, генерируемый источниками существенных неисправностей, часто изменяет общий уровень шума незначительно.
Результаты измерения уровня шума подвержены влиянию внешних условий, например уровень шума генерируемого машиной в значительной степени зависит от размеров и звукопоглощения помещений, где производят измерения, от наличия вблизи ОД другого оборудования, стен, а также от уровня посторонних шумов, влажности воздуха и т. д.
В связи с этим, уровень шума для характеристики технического состояния ОД используют очень редко, например, при оценке состояния однотипных ОД, если общий уровень шума и условия его измерений нормированы.
Большую информацию получают при измерениях спектра шума. На спектрограммах можно выделить характерные для составных частей ОД частотные полосы и по изменению их уровней определять состояние ОД. И даже при измерениях по спектрограммам отношение сигнала (измеряемого шума) к помехам для большинства ОД является слишком низким. Поэтому измерением спектра шума пользуются только для таких ОД, где уровень шума, несущего информацию о техническом состоянии, значительно превосходит уровень помех. К числу таких ОД относятся, например, газотурбинные двигатели и дизели (по системе выхлопа), которые генерируют интенсивные аэродинамические шумы. Путем измерения и анализа спектра шума газотурбинных двигателей выявляют выкрашивания беговых дорожек обойм подшипников, их несоосность, увеличение зазоров, выкрашивание и износ зубьев шестерен, а также дисбаланс роторов и другие дефекты.
Информацию можно увеличить путем периодического сравнения уровня или спектра шума одного ОД, если при этом внешние условия остаются неизменными.
1-исправный подшипник;
2- исправный подшипник, работающий в масле, содержащем металлическую стружку;
3-дефектный подшипник
Рисунок 61 – Изменение переходного электрического сопротивления подшипника №204 от частоты вращения
1-осевая нагрузка;
2-радиальная нагрузка
Рисунок 62 – Изменение относительной величины переходного электрического сопротивления подшипника №204 от нагрузки
На рисунке 63 показан спектр, включая 2-ю и 3-ю гармоники, для двухступенчатого редуктора, схема которого приведена на рисунке 64.
Допустимые уровни характеристических гармоник, а также общий уровень виброускорения устанавливаются для каждого вида ОД (зубчатых передач) на основании сопоставления данных, полученных специальными средствами измерений погрешности зубчатых колес и данных измерений уровней характеристических гармоник. При этом в зависимости от типа, назначения и размеров зубчатой передачи допускаются разные величины погрешностей зубчатых колес и соответственно различные общие уровни вибрации и уровни характеристических гармоник.
Рисунок 63 – Спектр характеристических гармоник двухступенчатого редуктора
Рисунок 64 – Схема двухступенчатого редуктора с обозначениями характеристических гармоник
Расчетом получают также характеристические гармоники подшипников качения. Отказы подшипников характеризуются разрушением сепаратора, износом шариков, проворачиванием наружной обоймы в корпусе и повреждением расточки корпуса подшипникового узла. Все эти процессы разрушения отражаются на спектрограммах изменением уровней целого ряда составляющих. На рисунке 65 показаны изменения уровней спектра характеристических гармоник виброперемещений при разрушении подшипника качения.
а – в начале эксплуатации;
б – после 42 ч работы;
в – после 57 ч работы перед разборкой
Рисунок 65 – Изменение спектра при разрушении подшипника
На рисунке 66 показана огибающая 1 фотограммы выходного сигнала акселерометра, полученной за один оборот сепаратора подшипника (без накопления) при fг = 5 Гц. Эта фотограмма показывает необходимость применения накопления для выявления сигналов, имеющих регулярный характер.
1-для одного оборота сепаратора;
2-накопленный сигнал;
3-накопленный сигнал при радиальном зазоре 0,1 мм
Рисунок 66 – Огибающие фотограмм вибросигналов подшипника при f=5 гц
Огибающая 2 фотограммы накопленного вибросигнала получена при тех же условиях. Здесь можно различить шесть пиков, соответствующих прохождению шариками зоны нагружения и характеризующих «податливость» подшипника. Огибающая 3 фотограммы накопленного вибросигнала изношенного подшипника (радиальный зазор 1 мм) качественно отличается от огибающей 2. Это связано с упорядочением ударов при прохождении зоны нагружения и отсутствием влияния гранности колец, что объясняется сошлифовыванием их поверхности и действием вибраций, вызванных ударами.
Опробирование сигнала. Соударения составных частей механических передач происходят в дискретные моменты цикла работы ОД. Для различных составных частей эти моменты, как правило, не совпадают, т. е. в цикле работы составной части можно найти такие интервалы, в которых будет наиболее полно проявляться генерируемый составной частью сигнал, выбранный в качестве диагностического параметра. Принцип выделения сигнала с частотой fi, генерируемого составной частью i ОД можно пояснить, используя рисунок 67. Выделение осуществляют с помощью синфазных циклу работы диагностируемой составной части стробирующих импульсов. При этом сигналы, проявляющиеся в других фазах цикла, подавляются. Формирование стробирующего импульса может происходить с помощью перестраиваемых одновибраторов, один из которых запускают от преобразователей угла поворота или линейного перемещения диагностируемой составной части ОД и регулируют фазу переднего фронта, а второй— ширину стробирующего импульса.
а-сигнал на выходе преобразователя;
б-стробирующий импульс длительностью τ;
в-выделенная часть сигнала
Рисунок 67 – Выделение части сигнала с помощью стробирующего импульса
7.2 Средства диагностирования
Средства измерения суммарных зазоров. Для измерения угловых и линейных зазоров применяют преобразователи перемещения. Схема простейшего прибора для работы с дифференциальным индуктивным преобразователем перемещения показана на рисунке 68. Схема предназначена для работы практически с любым типом индуктивного дифференциального преобразователя. Катушки L1 и L2 преобразователя вместе с обмотками трансформатора образуют схему моста. Мост балансируют резистором R2. Питание моста осуществляется от генератора на транзисторах VI и V2. Усиление сигнала на измерительной диагонали моста производится транзистором V3, в цепь коллектора которого включен фазовый детектор на диодах V4—V7.
Средства дифференцированного измерения угловых зазоров в многоступенчатых зубчатых передачах. Структурная схема устройства для дифференцированного измерения угловых зазоров показана на рисунке 69. Приводной электродвигатель 1 мощностью 0,001...0,05N (где N—номинальная мощность, передаваемая диагностируемым редуктором), через волновой редуктор 2 с передаточным числом 1000...3000 механически соединен с выходным валом диагностируемого редуктора 4 через муфту 3, включающую в себя тензорезисторный преобразователь крутящего момента.
Рисунок 68 – Схема люфтомера с дифференциальным индуктивным преобразователя перемещения
Рисунок 69 – Схема устройства для дифференцированного измерения угловых зазоров многоступенчатого редуктора
Средства диагностирования зубчатых передач по силовым параметрам. Для измерения сил, действующих в двух взаимно-перпендикулярных плоскостях на опоры подшипников, могут быть использованы различные типы силоизмерителей. Применение тензометрических стержневых силоизмерителей показано на рисунке 70. Опора подшипника 2 (рисунок 70, а) присоединена к станине через два стержневых силоизмерителя 1. Силоизмерители (рисунок 70, б) имеют сечение двутавров – это сделано для снижения погрешности измерения сил за счет изгибных деформаций сило-измерительных стержней. С этой же целью на противоположные стенки стойки двутавра наклеено по два тензорезистора 3. Каждая пара тензорезисторов 3 соединена последовательно и включена в одном из плеч полумостовых схем. Выходы полумостовых соединены с усилителями 4 (рисунок 70, в). Выходы усилителей подключены к вертикальному и горизонтальному входам ЭЛО, на экране которого можно наблюдать фигуры Лиссажу и измерять наклоны их осей, характеризующие силы, действующие в диагностируемом зацеплении.
Средства диагностирования по общему уровню вибраций. На рисунке 71 показаны структурные схемы приборов, применяемых при диагностировании машин по уровню параметров вибраций. Прибор (рисунок 71, а) работает с индукционным велосиметром 1, который через полосовой фильтр 2 соединен с квадратичным детектором 3. К выходу детектора подключен стрелочный прибор 5 для измерения уровня виброскорости и пороговое устройство 4 с регулируемым порогом срабатывания и световым индикатором превышения установленного уровня виброскорости. Через вывод 9 к выходу полосового фильтра можно присоединять регистратор уровня.
Прибор (рисунок 71, б) работает с пьезоэлектрическим акселерометром 6. Его схема имеет согласующий усилитель 7 и интегратор 8. К выводам 9 можно присоединять регистрирующий прибор для записи широкополосных или проинтегрированных и отфильтрованных сигналов. Полосовые фильтры в этих приборах имеют обычно относительно широкую полосу пропускания, их устанавливают только с целью снижения уровня вибрационных и приборных помех.
Средства виброакустического спектрального анализа. Данные приборы имеют весьма широкое применение при различных акустических измерениях и при исследованиях вибраций. В технической диагностике эти приборы могут быть использованы для получения «механических подписей» ОД. На рисунке 72 показана структурная схема анализатора последовательного действия типа 2121, схема которого типична для анализаторов спектра средней сложности. К входному гнезду 1 анализатора может быть присоединен выход предусилителя акселерометра или микрофона. Усиление сигнала в приборе осуществляется пятикаскадным усилителем 3, который отличается низким уровнем собственного шума и малыми нелинейными искажениями. Общий коэффициент усиления пяти каскадов усилителя составляет 120 дБ и может регулироваться двумя аттенюаторами 2 ступенчато через 10 дБ. Благодаря этому диапазон измерения входных сигналов по уровню находится в пределах от 10 мкВ до 300 В. После выходного усилителя установлен индикатор перегрузки 4. Входной усилитель по выбору оператора с помощью переключателя 9 может быть соединен е-выходным усилителем: непосредственно для измерения общего уровня; через перестраиваемый с помощью переключателя 7 полосовой фильтр 8; перестраиваемые фильтры: заградительный 10, верхних частот 11 или нижних частот 12. Через гнезда 5 к прибору подключают внешние фильтры. Все четыре вида фильтров, установленных в приборе, активные (на операционных усилителях) и рассчитаны на диапазон измерений по частоте 20 Гц...20 кГц.
Полосовой фильтр 8 может работать с неизменными относительными полосами пропускания: 1,3 и 10% или V3 октавы. Избирательность полосового (рисунок 73, а) фильтра равна соответственно 70, 65, 45 и 30 дБ/октава. Заградительный фильтр (рисунок 73, б) имеет ослабление не менее 40 дБ на частоте настройки. Фильтры верхних и нижних частот (рисунок 73, б, в) обеспечивают на частоте настройки ослабление около 3 дБ, при крутизне характеристик 24 дБ/октава. Настройка фильтров может быть осуществлена как вручную, так и автоматически с приводом от самописца уровня.
Для градуировки прибора в его схеме предусмотрен источник прямоугольных импульсов 6 (см. рисунок 72), которые формируются из сетевого напряжения 50 Гц с помощью стабилитронов.
Индикация уровня осуществляется с помощью стрелочного прибора 16, который подключен к квадратичному детектору 15, или с помощью самописца уровня включаемого на выход оконечного усилителя 13 через гнезда 14.
Рисунок 70 – Применение тензометрических стержневых силоизмерителей для измерения реакции, действующих на опоры подшипника
Рисунок 71 – Структурные схемы встроенных приборов для измерения уровней параметров вибрации
Рисунок 72 – Структурная схема последовательного анализатора спектра типа 2121
Рисунок 73 – АЧХ фильтров анализатора спектра 2121
На рисунке 74, а показана структурная схема прибора, в которой использован первый из названных способов следящей подстройки частоты. Сигнал с частотой fс с выхода предусилителя 2 вибропреобразователя 1 поступает одновременно на относительно широкополосовой фильтр 3 измерительного тракта и на вход фильтра опорной частоты 8, с помощью этого фильтра выделяется сигнал с опорной частотой fоп. Сигнал опорной частоты далее поступает на умножитель частоты 9 с коэффициентом умножения n.
Приборы, в которых фильтр перестраивается от преобразователя частоты вращения, допускают более широкие пределы измерения частоты вращения. Структурная схема прибора (рисунок 74, б) имеет преобразователь частоты вращения 10, сигнал от которого через умножитель частоты 9 и смеситель 4 поступает для настройки фильтра промежуточной частоты 5.
а – от измеряемого сигнала;
б – от преобразователя частоты вращения ОД
Рисунок 74 – Структурные схемы приборов со следящими узкополосными фильтрами для измерения виброускорении при настройке
Известны и другие структурные схемы анализаторов со следящей фильтрацией.
Прибор для реализации метода кинематической синхронизации. Схема прибора показана на рисунке 75. На ОД 6 установлены вибропреобразователь (акселерометр) 7 и преобразователь 5 угла поворота вала.
Сигнал с акселерометра поступает на переключатель S1. В верхнем положении переключателя акселерометр соединен со входом предусилителя /. Выход последнего соединен с амплитудным селектором 2, полосовым фильтром 9 и интегратором 8. На вертикальный вход ЭЛО 3 через детектор V с помощью переключателя S2 может быть подключен выход одного из перечисленных выше устройств. К горизонтальному входу ЭЛО присоединен преобразователь координаты (угла поворота вала), обеспечивающий синхронизацию развертки с частотой вращения вала ОД. Для регистрации фотограммы ЭЛО оборудован фотоприставкой 4. Для градуировки прибора к его входу с помощью переключателя S/ подключают генератор звуковых частот 10.
Виброускорение измеряют акселерометром любого типа. Сигнал координаты лучше всего получать от фотоэлектрического преобразователя, работающего на «просвет» или на отражение. Одна из схем включения фотоэлектрического преобразователя координаты на фотодиоде показана на рисунке 76.
Средства диагностирования стальных канатов. На рисунке 77 показаны схемы приборов для определения локальных дефектов (обрывов проволок) по длине каната. В приборе постоянного тока (рисунок 77, а) канат 3, проходя через катушки, намагничивается. Катушка намагничивания 2 состоит из двух идентичных частей, включенных встречно, что позволяет скомпенсировать ЭДС, наведенную в измерительной катушке 1 при изменении скорости каната, поэтому на входе усилителя 4 действует ЭДС, определяемая неоднородностью сечений каната, проходящего через катушку.
Однако абсолютное значение ЭДС зависит от скорости движения каната 3. Независимость ЭДС от скорости движения каната и большую чувствительность к дефектам имеют схемы прибора на переменном токе (рисунок 77, б). Здесь намагничивающая катушка 2 питается переменным током, а части измерительной катушки 1 образуют два смежных плеча измерительного моста. Мост балансируют с помощью резистора R на участке каната с равномерным сечением. Напряжение на входе усилителя 4 не зависит от скорости и определяется только различием в сечении участков каната, находящихся в частях измерительной катушки. В качестве индикатора в обоих приборах используют самописцы или осцилллографы 5, число импульсов на выходе параллельно регистрируют электромеханические счетчики 6.
На рисунке 78, а показан вид импульса на выходе прибора при прохождении каната с оборванной проволокой (рисунок 78, б) измерительной катушки. Скорость протяжки ленты самописца или осциллографа синхронизируют со скоростью каната, или от специального преобразователя на ленту наносят метки длины проходящего каната. В ряде случаев более полную информацию о прочности каната дает суммарная величина сечения, а не число оборванных проволок. Для диагностирования канатов по величине уменьшения сечения используют приборы с индуктивными преобразователями.
Конструкции индуктивных преобразователей для диагностирования канатов приведены на рисунке 79. Преобразователь (рисунок 79, а) представляет собой катушку, сердечником которой является диагностируемый канат. При изменении сечения каната меняется индуктивность катушки, так как примерно V3 часть пути магнитные силовые линии проходят через канат. Этот преобразователь прост по конструкции и имеет достаточно высокую чувствительность, но его применение ограничено необходимостью расчалки конца каната или намотки катушки преобразователя непосредственно на диагностируемом канате. Поэтому наибольшее распространение получили преобразователи с разъемным магнитопроводом (рисунок 79, б). На концах П-образных магнитопроводов обычно устанавливают башмаки, имеющие профиль полуокружности; такая форма башмаков позволяет получить наиболее равномерную информацию об уменьшении сечения по всей площади поперечного сечения каната.
Для измерений с индуктивными преобразователями применяют схемы резонансных мостов с усилителями (рисунок 80).
Преобразователь включают в одно из плеч измерительного моста 3, где вместе с емкостью С образуется контур, настроенный на частоту питающего напряжения. Мост балансируется при установке в ярме 2 преобразователя неизношенного отрезка каната номинального сечения. При проходе через ярмо преобразователя участка каната 1 с меньшим сечением на измерительной диагонали моста появляется напряжение, которое усиливается усилителем 4, детектируется и поступает на стрелочный индикатор 5, отградуированный в процентах потери сечения.
Оптимальная частота питающего моста напряжения 25—30 Гц, при большей частоте начинает влиять поверхностный эффект, что, в свою очередь, ведет к уменьшению информации о потерях сечения во внутренних проволоках каната.
Однако, учитывая сложность создания низкочастотных генераторов, а также повышение уровня помех при питании моста током низкой частоты, используют сетевую частоту 50 Гц, хотя уже и при таком значении частоты заметно уменьшается чувствительность прибора к изменениям рабочего сечения в областях, расположенных около центра сечения каната.
Недостаток схемы резонансного моста состоит в том, что даже небольшие изменения частоты заметно влияют на чувствительность прибора, поэтому применяют двухмостовые схемы, измеряемый сигнал в этих схемах снимается с диагоналей двух последовательно включенных мостов, один из которых выполняет функции пассивного. В этой схеме уровень измеряемого сигнала значительно меньше зависит от частоты питающего напряжения. Кроме того, двухмостовая схема практически полностью компенсирует напряжение высших гармоник, проявляющихся от несинусоидальности питающего напряжения и нелинейности стальных сердечников. На рисунке 81 показана схема прибора для диагностирования стальных канатов. Измеряемый сигнал снимается с потенциометра R и усиливается усилителем на транзисторах VI и V2. Выход усилителя нагружен индикатором через детектор V5. Усилитель охвачен отрицательной обратной связью.
В схеме прибора имеется реле предельного износа на транзисторах V3 и V4. В коллектор транзистора V4 включена лампа Л, сигнализирующая о предельном износе.
Рисунок 75 – Схема прибора реализации метода кинематической синхронизации
Рисунок 76 - Схема включения фотоэлектрического преобразователя координаты
Рисунок 77 – Структурные схемы приборов для диагностирования стальных канатов
а-осциллограмма дефекта;
б- дефектный канат;
1-дефект;
2-отметка длины
Рисунок 78 – Обнаружение оборванных проволок в канате
Рисунок 79 – Конструкции индуктивных преобразователей для диагностирования каната
Рисунок 80 – Структурная схема прибора с индуктивным преобразователем
Рисунок 81 – Принципиальная схема прибора для измерения потери сечения стальных канатов
Литература
1 Шляндин В.М., Мартяшин А.И. Автоматический контроль радиоэлектронного и электротехнического оборудования. – М. : Энергия, 1972. – 264 с.
2 Барсуков Ф.И., Русанов Ю.Б. Элементы и устройства радиотелеметрических систем. – М. : Энергия, 1973. – 256 с.
3 Биргер И.А. Техническая диагностика. – М. : Машиностроение, 1978. – 240 с.
4 Гаскаров Д.В., Голинкевич Т.А., Мозгалевский А.В. Прогнозирование технического состояния и надежности радиоэлектронной аппаратуры. – М. : Советское радио, 1974. – 224 с.
5 Дворяшин Б.В., Кузнецов Л.И. Радиотехнические измерения. – М. : Советское радио, 1978. – 360 с.
6 Загоруйко Н.Г. Методы распознавания и их применение. – М. : Советское радио, 1972. – 210 с.
7 Квалиметрия и диагностирование механизмов. – М. : Наука, 1979. – 134 с.
8 Костенко С.И., Черейский П.М. Технология диагностирования тракторов на основе перспективных методов и средств автоматизированного контроля. Гидросистемы и приводы машин для хлопководства. Труды ТИИМСХ. – Ташкент, 1978, вып. 95. – С. 34-44.
9 Кулаковский В.Б. Профилактические испытания и дефекты изоляции крупных электрических машин. – М. : Энергия, 1970. – 184 с.
10 Макаров Р.А. Средства технической диагностики машин. – М. : Машиностроение, 1981. – 223 с.
11 Макаров Р.А. Гидротестеры. – Механизация строительства, 1979. – №6. – С. 20 – 23.
12 Методика диагностирования эвольвентных цилиндрических зубчатых передач и цилиндрических передач Новикова по их виброакустическим свойствам методом характеристических гармоник. – Горький, ВНИИНМАШ ГФ, 1976. – 18 с.
13 Методические указания по прогнозированию технического состояния машин. – М. : ОНТИ ГОСНИТИ, 1972. – 216 с.
14 Мирский Г.Я. Радиоэлектронные измерения. Изд. 3-е. – М. : Энергия, 1975. – 600 с.
15 Нейман В.Г. Надежность объемных гидроприводов и их элементов. – М. : Машиностроение, 1977. – 167 с.
16 Нахапетян Е.Г. Определение критериев качества и диагностирование механизмов. – М. : Наука, 1977. – 140 с.
17 Одинец С.С., Топилин Г.Е. Средства измерения крутящего момента. – М. : Машиностроение, 1977. – 160 с.
18 Основы технической диагностики. В 2-х кн. Кн.1. Модели объектов, методы и алгоритмы диагноза / Под ред. П.П. Пархоменко. – М. : Энергия, 1976. – 464 с.
19 Самбурский А.И. Бесконтактные измерения параметров вращающихся объектов (Б-ка приборостроителя). – М. : Машиностроение, 1979. – 141 с.
20 Техническая диагностика: Сборник трудов / Под ред. П.П. Пархоменко. – М. : Наука, 1973. – 368 с.
21 Тун А.Я. Наладка электрических машин электроприводов. – М.: Энергия, 1970. – 192 с.
Содержание
Введение………………………………………………………………3
1 Практическая работа №1. Основные свойства средств
технической диагностики машин..…………………………………..4
2 Практическая работа №2. Первичные измерительные
преобразователи СТДМ……………………………………………..11
3 Практическая работа №3. Конструкции первичных
преобразователей, применяемые в СТДМ…………………………30
4 Практическая работа №4. Средства диагностирования
электрического привода и электрооборудования машин…………47
5 Практическая работа №5. Средства диагностирования
двигателей внутреннего сгорания…………………………………..58
6 Практическая работа №6. Средства диагностирования
гидравлического привода машин……………………………………71
7 Практическая работа №7. Средства диагностирования
механических передач машин……………………..………………...91
Литература…………………………………………………………..112
РЕЦЕНЗИЯ
на сборник методических указаний к практическим работам по дисциплине «Системный анализ и диагностирование технических объектов», Р.О. Олжабаев, К.Н. Ромасёв, Д.А. Искакова, Павлодар, 2007. – 114 с.
В сборнике методических указаний излагаются основные свойства средств технической диагностики машин, принципы действия различных первичных измерительных преобразователей СТДМ. Постановка задачи, формирование множества возможных вариантов решения задачи. Анализ ресурсного обеспечения вариантов; разработка вариантов; выбор и обоснование критериев эффективности решения задачи; методы и алгоритм принятия решения о выборе рационального варианта решения задачи.
Эффективность средств технической диагностики машин (СТДМ) не может быть рассмотрена в отрыве от эффективности системы диагностирования, в которой они используются. Эффективность, в свою очередь, является наиболее общей характеристикой системы диагностирования, оценивающей совершенство выполняемых ею функций.
При изложении материала использован системный подход, обеспечивающий возможность выявить причины использования различных преобразователей.
В сборнике методических указаний даны рекомендации по порядку выполнения практических работ.
Сборник методических указаний является составной частью в общем цикле работ, выполняемых по дисциплине «Системный анализ и диагностирование технических объектов».
Рецензент, профессор Н.С. Дудак
РЕЦЕНЗИЯ
на сборник методических указаний к практическим работам по дисциплине «Системный анализ и диагностирование технических объектов»
В сборнике методических указаний излагаются понятия о конструктивном оформлении первичных преобразователей применительно к конкретным диагностируемым объектам, методы диагностирования и конструкции средств диагностирования электропривода и электрооборудования машин.
Важнейшей задачей является создание диагностических средств, обеспечивающих локализацию дефектов и прогнозирование ресурса изоляции обмоток электрических машин и аппаратов. Эта задача может быть решена только в результате поиска новых диагностических параметров и методов диагностирования.
Особую актуальность средства диагностирования ДВС приобрели в связи с возникшими проблемами экономии топлива и охраны окружающей среды, поскольку именно от технического состояния двигателей зависит как топливная экономичность, так и количество и состав загрязняющих веществ в отработавших газах. В связи с этим, приборы для анализа состава отработавших газов, входящие в комплекты средств, подверглись значительному усовершенствованию в части чувствительности, точности и расширения получаемой информации об элементном составе.
При изложении материала использован системный подход, обеспечивающий возможность выявить причины использования различных преобразователей.
В сборнике методических указаний даны рекомендации по порядку выполнения практических работ.
Сборник методических указаний является составной частью в общем цикле работ, выполняемых по дисциплине «Системный анализ и диагностирование технических объектов».
Рецензент, профессор И.А. Шумейко
Ф СО ПГУ 4.05.2/08 Министерство образования и
науки Республики Казахстан
Павлодарский государственный
университет им. С. Торайгырова
кафедра машиностроения и
стандартизации
ВЫПИСКА ИЗ ПРОТОКОЛА №10
заседания методического семинара
от «4» мая 2007 г.
г. Павлодар
Председательствующий: к.т.н., профессор И.А. Шумейко
Секретарь: ассистент Д.А. Искакова
ПОВЕСТКА ДНЯ:
-
На утверждение и предоставление к изданию в НИЦ предоставлены методические указания к выполнению практических работ.
СЛУШАЛИ: К.т.н., профессор Р.О. Олжабаев, К.Н. Ромасёв, ассистент Д.А. Искакова
К утверждению были предоставлены методические указания к выполнению практических работ по дисциплине «Системный анализ и диагностирование технических объектов» для студентов машиностроительных специальностей.
ПОСТАНОВИЛИ: Утвердить и предоставить к изданию в НИЦ методические указания к выполнению практических работ по дисциплине «Системный анализ и диагностирование технических объектов» для студентов машиностроительных специальностей.
Председательствующий,
к.т.н., профессор______________________________И.А. Шумейко
Секретарь,
магистр, ассистент____________________________________Д.А. Искакова
в дело №_22-04-03_
страница 1 ... страница 5 | страница 6 | страница 7 страница 8
|