страница 1 ... страница 2 | страница 3 страница 4 страница 5 ... страница 7 | страница 8
3.2 Преобразователи сил (силоизмерители)
При диагностировании машин определение сил производят двумя способами: измерением деформаций, пропорциональных действующим в составных частях ОД силам, и получением сигналов от специальных преобразователей сил, встраиваемых в разрыв силовых цепей ОД или воспринимающих реактивные силы.
Первый способ измерения сил реализуют при встроенных средствах, например наклеенных на ОД в процессе изготовления тензорезисторов.
Второй способ измерения сил широко используют в различных диагностических стендах для измерения реактивных сил, воспринимаемых стендами от ОД, а также для измерения усилий на рычагах и педалях управления ОД. Реже силоизмерители применяют для измерения сил в составных частях ОД, поскольку это связано с частичной разборкой ОД.
На рисунке 15 показаны конструкции тензорезисторных силоизмерителей, применяемых в СТДМ.
3.3 Преобразователи давлений
В СТДМ используют преобразователи давлений, основанные на следующих способах определения давления: по деформациям стенок трубопроводов и шлангов или стенок корпусов гидро- и пневмооборудования, которые измеряют с помощью специальных прижимных преобразователей, и по деформациям, перемещениям или силам на упругих чувствительных элементах, установленных на ОД постоянно или только на время диагностирования.
а – для растягивающих сил
б, в – для сжимающих сил
1 – тензорезисторы
2 – чувствительный элемент
3 – опорные диски
Рисунок 15 – Конструкции тензорезисторных силоизмерителей
На рисунке 16 показана одна из конструкций преобразователя для измерения давления по деформациям наружных стенок трубопровода или шланга. Основу преобразователя составляет двухрычажный зажим 4. В дугообразных впадинах рычагов с радиусами, соответствующими размерах трубопровода ОД, установлены прокладки 2 из эластичного материала; на поверхностях этих прокладок, обращенных к трубопроводу, наклеены тензорезисторы 3 основой наружу.
Рисунок 16 – Преобразователь давления
После установки преобразователя тензорезисторы прижимаются к трубопроводу 1 усилием пружины 5, соединяющей противоположные концы рычагов. Для улучшения передачи деформаций на основу тензорезисторов, прилегающую к ОД, наносят с помощью клея слой абразивного порошка.
На рисунке 17, а показаны индуктивный, а на рисунке 17, б тензорезисторный преобразователи давления с плоскими мембранами. Серийно выпускают индуктивные преобразователи давления типов ДД-11 и ДИ и тензорезисторные типов ЛХ-412 и ЛХ-415. Специально для СТДМ выпускают тензорезисторные преобразователи типа ИПД-2.
Гофрированные мембраны отличаются от плоских большими допустимыми прогибами. Характеристики гофрированных мембран определяются отношениями толщин мембран к глубинам гофров. С увеличением толщины мембраны возрастают ее жесткость и нелинейность градуировочной зависимости. Увеличение глубины гофров улучшает линейность, но повышает жесткость мембраны при малых прогибах, что сокращает диапазон измерений. Большинство гофрированных мембран имеет краевые гофры, отличающиеся по размерам и форме от остальных, что позволяет увеличить до 3 раз допустимый прогиб мембраны.
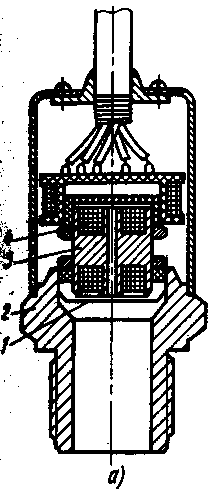
а – индуктивный мембранный
б – тензорезисторный мембранный
в, г – тензорезисторные с цилиндрическим упругим элементом
1 – мембрана
2 – корпус
3 – якорь
4 – катушки
5 – тензорезисторы
6 – упругий чувствительный элемент
7 – центральный стержень
Рисунок 17 – Преобразователи давления
На рисунке 17, в показан разрез цилиндрического преобразователя давления с тензорезисторами, наклеенными поперек образующей.
Для уменьшения рабочего объема цилиндрического преобразователя давления, что необходимо, например, при измерениях давлений в камерах сгорания двигателей, внутри чувствительного элемента размещают сплошной цилиндр меньшего диаметра, чтобы обеспечить небольшие зазоры между внутренними стенками чувствительного элемента и поверхностью сплошного цилиндра (рисунок 17, г).
3.4 Преобразователи расхода
Расходомер переменного перепада давления содержит диафрагму 1 (рисунок 18, а), сужающую сечение, в котором из-за повышения средней скорости часть потенциальной энергии потока переходит в кинетическую. В результате статическое давление падает, по измеренной дифференциальным преобразователем 2 разности давлений до диафрагмы и после нее находят объемный расход.
Из числа расходомеров обтекания в СТДМ применяют ротаметры (рисунок 18, б). Их выполняют в виде конической трубки, внутри которой расположен поплавок 3 (обтекаемое тело), поддерживаемый в равновесном состоянии движущимся снизу потоком жидкости. Равновесие поплавка поддерживается автоматически, за счет изменения площади проходного сечения при перемещении поплавка от изменения сил воздействия потока.
К расходомерам обтекания, применяемым в СТДМ, относятся и расходомеры с поворотной лопастью (рисунок 18, в). Поворотная лопасть воспринимает силовое воздействие набегающего потока жидкости, расход которой определяют, и поворачивается или изгибается на угол, пропорциональный величине расхода. Силам, действующим со стороны потока, противодействует усилие, развиваемое противодействующей пружиной или упругим чувствительным элементом 5 (рисунок 18, в).
В тахометрических расходомерах движущийся поток жидкости приводит во вращение ротор или шарик (по периферии трубопровода). Частота вращения ротора или шарика является мерой расхода жидкости, протекающей через расходомер.
В турбинно-тахометрических расходомерах (рисунок 18, г) установлена миниатюрная аксиальная или тангенциальная турбинка 7. Шариковые тахометрические расходомеры (рисунок 18, д) имеют свободновращающийся шарик 9, который приводится во вращение от предварительной закрутки потока на неподвижном винтовом шнеке или в тангенциальной камере.
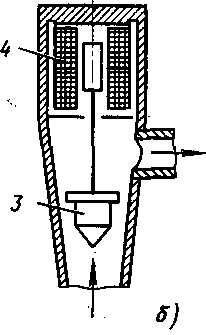 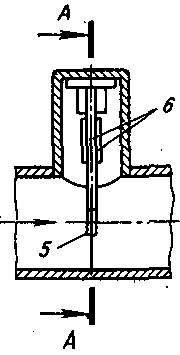
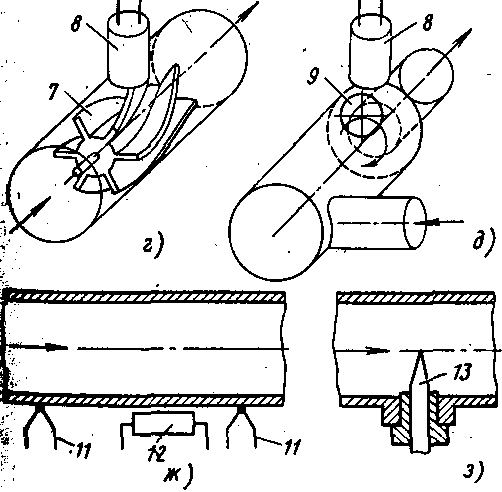
Рисунок 18 – Схемы преобразователей расхода
Для использования в качестве расходомера гидромотора (рисунок 18, е) на его выходном валу 10 устанавливают индукционный или фотоэлектрический преобразователь частоты вращения 8.
Тепловые расходомеры. В СТДМ применяют две разновидности тепловых расходомеров: калориметрические с внешним нагревом и пленочные термоанемометрические. В первых (рисунок 18, ж) на поверхности трубопровода устанавливают нагреватель 12 и два термопреобразователя 11, например термопары.
Термоанемометрические тепловые расходомеры (рисунок 18, з) основаны на зависимости между количеством тепла, теряемым непрерывно нагретым чувствительным элементом, размещенным непосредственно в жидкости, и скоростью этой жидкости.
Одна из конструкций ультразвукового расходомера показана на рисунке 18, и. пьезопреобразователи 14 и звукопроводы 15 расположены на поверхности трубопровода. Преломление ультразвуковых колебаний в этой конструкции происходит на границах преобразователь – трубопровод и преобразователь – жидкость. Углы преломления и скорость звука зависят от изменения температуры, давления и плотности жидкости, однако для измерений относительных значений расходов при фиксированных температурах определенных режимов диагностирования ОД эти погрешности являются систематическими и могут быть легко учтены.
3.5 Преобразователи температуры
В СТДМ применяют практически все виды электрических преобразователей температуры. Для измерения температур рабочих жидкостей в гидросистемах используют термопары (рисунок 19, а) и преобразователи на основе термисторов (рисунок 19, б). Термопара 1 и термистор 3 помещены в защитных корпусах 2. Термопара в данном случае позволяет производить локальные измерения температуры, а преобразователь с термистором применяют для измерения средней температуры потока.
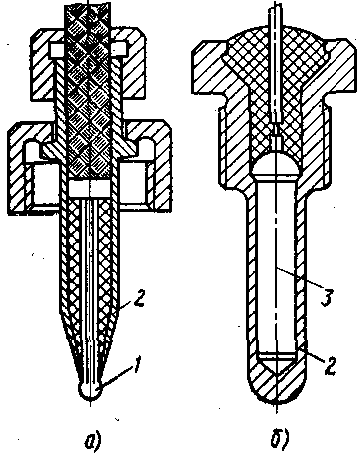
Рисунок 19 – Конструкции термопреобразователей
Для измерения температур поверхностей используют преобразователи с платиновыми термометрами сопротивления (рисунок 19, в). Чувствительным элементом преобразователя является плоская спираль 4 из платиновой проволоки диаметром 0,05 мм, покрытая лаком. На основе этой конструкции промышленность выпускает преобразователи типа ТСП со стандартной градуировкой (гр. 21, 22) для измерения температур в подшипниках. Подобную конструкцию имеют медные термометры типа ТСМ со стандартной градуировкой (гр. 23, 24).
Измерение температур поверхностей ОД из ферромагнитных материалов можно осуществлять с помощью термопар или термисторов 3, размещенных в кольцевых магнитах 4 (рисунок 19, г). Постоянную силу прижатия преобразователя к поверхности ОД обеспечивает миниатюрная гофрированная мембрана 5.
3.6 Преобразователи встроенных СТДМ
Встроенные СТДМ можно разделить на три группы: постоянно установленные на ОД первичные преобразователи, рассчитанные на подключение внешних промежуточных преобразователей и приборов; установленные на ОД первичные преобразователи, объединенные с промежуточными преобразователями; полный встроенный измерительный комплект, включающий в себя сигнализирующие или показывающие приборы.
На рисунке 20 показаны варианты установки встроенных преобразователей в корпусе подшипника качения, например акселерометра 1 (рисунок 20, а) в специальном канале корпуса подшипника качения. Расположение вибропреобразователя в непосредственной близости от обоймы подшипника существенно повышает отношение сигнал – помеха за счет фильтрующих свойств конструкций ОД.
Еще большее отношение сигнал – помеха обеспечивают преобразователи, измеряющие не виброускорение, а виброперемещение, пропорциональное прогибу (или деформации) тонких стенок, образованных гнездом подшипника и проточками в корпусе подшипникового узла (рисунок 20, б и в). При этом практически полностью исключается влияние низкочастотных колебаний всего ОД, к которым чувствительны акселерометры.
Для выделения нерегулярных сигналов, которые характерны для ранних стадий разрушения подшипников качения, применяют по два преобразователя, включенных в дифференциальную схему (рисунок 20, в). Благодаря этому происходит компенсация (в значительной степени) на выходе схемы регулярной составляющей сигнала. Для встроенного измерения виброускорений в соответствии с рисунком 20, а могут быть использованы пьезоэлектрические акселерометры конструкций, показанных на рисунке 13.
а – пьезоэлектрический акселерометр
б – тензорезисторный для измерения виброперемещений
в – индукционный для измерений виброскорости
1 – акселерометр
2 – тензорезистор
3 – упругий элемент
4 – индукционные преобразователи
Рисунок 20 – Установка встроенных преобразователей в корпусе подшипника качения
При диагностировании по тепловым параметрам в качестве встроенных могут быть использованы преобразователи температуры (рисунки 19, а-в).
На рисунке 21 показана конструкция дифференциального индуктивного преобразователя давления, который можно использовать с калиброванными диафрагмами как встроенный расходомер для гидросистем. Этот преобразователь прост по конструкции, отличается малыми размерами и высокой надежностью.
При установке тензорезисторов в качестве встроенных преобразователей предъявляются жесткие требования к защите их от воздействия влаги, масла и грязи. На рисунке 22 показаны способы защиты тензорезисторов. Сопротивление изоляции в значительной степени определяет состояние хорошо наклеенного тензорезистора, поэтому необходимо выполнять периодические проверки этого параметра.
Примером простого встроенного преобразователя с выходом на сигнальное устройство является специальная сигнальная колодка для подъемно-транспортных машин. Преобразователи 1 (чувствительные элементы) предельных износов устанавливают в тело тормозной наладки 2 на определенной глубине (рисунок 23, а). Чувствительный элемент представляет собой пробку, изготовленную из изоляционного материала. Конусную часть пробки охватывает тонкая проволока или фольга 3, ее выводные концы 4 пропущены через тело пробки (рисунок 23, б). Установленные на тормозной накладке преобразователи соединяют последовательно, а параллельно им включают сигнальную лампочку (рисунок 23, в), через резистор эту цепь включают в цепи питания электрического привода машины. При истирании проволоки или фольги лампочка загорается, сигнализируя о достижении предельного износа. Такая схема включения лампочки повышает надежность сигнализации, так как исключает необходимость применения реле или преобразователей, работающих на замыкание цепи.
1 – катушка
2 – мембрана
Рисунок 21 – Дифференциальный индуктивный преобразователь давления для измерения расходов
На рисунке 24 показан пример установки преобразователя давления 1 на переходном устройстве, выполненного в виде штуцера 2, который установлен в топливопроводе форсунки дизельного ДВС. После вывинчивания преобразователя давления в резьбовое отверстие штуцера ввинчивают пробку 3.
Другое встроенное переходное устройство предназначено для установки в гидравлических системах экскаваторов блока преобразователей. Устройство выполнено в виде патрубка (рисунок 25), на внутренней поверхности которого имеются асимметричные пазы.
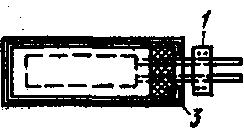
а – при работе в проводящей среде
б – при повышенной влажности
в – с дополнительной защитой от механических повреждений
1 – переходная колодка для выводов
2 – резиновый колпачок
3 – уплотнение
4 – гидрозащитный слой
5 – металлический колпачок
Рисунок 22 – Защита тензорезисторов при использовании их в качестве встроенных преобразователей
Рисунок 23 – Устройство для определения допустимых износов тормозных накладок
Поршень 1, вставленный в патрубок, имеет выступы, которые входят в пазы. В теле поршня сделаны замковые пазы для его соединения с заглушкой или блоком преобразователей. При работе гидропривода заглушка 2, зафиксированная накидной гайкой 3, удерживает поршень в верхнем положении. При подготовке к диагностированию накидную гайку отвинчивают, вынимают заглушку и на ее место устанавливают блок преобразователей 4, который предварительно соединяют с замковым устройством поршня. После завинчивания накидной гайки блока преобразователей проводят диагностирование. Применение такого устройства существенно снижает трудоемкость диагностирования и практически исключает утечки жидкости и загрязнение гидросистемы.
Рисунок 24-Установка преобразователя давления на форсунке дизельного двигателя
а – с заглушкой
б – с блоком преобразователей
Рисунок 25 - Встроенное устройство для включения блока преобразователей в гидравлическую систему
Практическая работа №4 Средства диагностирования электрического привода и электрооборудования машин
Цель работы: Изучение содержания методов диагностирования и конструкции средств диагностирования электропривода и электрооборудования машин.
Задачи работы: Научить студентов планировать и осуществлять диагностирование электропривода и электрооборудования машин.
После выполнения работы студент должен
Знать: сущность рассмотренных методов диагностирования электропривода и электрооборудования машин, области применения данных методов.
Уметь: назначать соответствующие методы и средства диагностирования применительно к диагностируемым параметрам электропривода и электрооборудования машин.
Приборы для измерения основных электрических величин и некоторых параметров электрических цепей были созданы раньше, чем электрический привод и электрооборудование машин. Средства измерения электрических величин и параметров электрических цепей значительно развились в направлении точности, быстродействия и расширения номенклатуры измеряемых величин, однако это не внесло столь же значительных изменений в возможности диагностирования.
Общими недостатками существующих средств диагностирования, не требующих разборки элементов ОД, является невозможность локализации дефектов, а также низкая чувствительность к состоянию ОД. Например, локальные дефекты изоляции электрической машины, которые, развиваясь, могут вызвать пробой, вносят сравнительно малый вклад в общее снижение сопротивления изоляции или изменения других параметров. Существующие средства позволяют главным образом осуществлять поиск неисправностей, и определять состояние ОД, а также прогнозировать остаточный ресурс с очень низкой вероятностью.
Сейчас интенсивно ведутся исследования в области неразрушающих методов и средств контроля составных частей и элементов радиоэлектронной аппаратуры. Некоторые из этих средств в связи с общностью процессов деградации составных частей радиоэлектронных устройств и составных частей электрического привода и электрооборудования машин принципиально могли бы быть использованы для диагностирования последних. Однако пока эти средства сложны, и их применение ограничено в основном исследовательскими задачами. Кроме того, большая часть этих средств, базирующихся на эффективных неразрушающих методах (ИК интерферометрия, ИК элипсометрия, измерение отражения когерентного света и др.), обеспечивает оценку состояния ОД без разрушения только условно. Например, применение этих средств не вызывает разрушений полупроводникового перехода транзистора, но требует разгерметизации его корпуса, что неприемлемо для эксплуатационной диагностики.
Важнейшей задачей является создание диагностических средств, обеспечивающих локализацию дефектов и прогнозирование ресурса изоляции обмоток электрических машин и аппаратов. Эта задача может быть решена только в результате поиска новых диагностических параметров и методов диагностирования.
К числу других задач, связанных с развитием средств диагностирования электрического привода и электрооборудования машин, относятся:
- развитие средств диагностирования полупроводниковых элементов схем (диодов, транзисторов, тиристоров и др.) позволяющих производить диагностирование без отсоединения этих элементов;
- разработка средств диагностирования электромеханических систем аппаратов, используемых в приводе и электрооборудовании машин;
- разработка унифицированного ряда встроенных преобразователей для электрических цепей, которые должны отличаться простотой, высокой надежностью и низкой стоимостью;
- создание унифицированных приборов на основе виброаккустических методов для диагностирования подшипников электрических машин;
- разработка автоматизированных средств диагностирования системы электрического привода на основе метода функциональных циклограмм.
страница 1 ... страница 2 | страница 3 страница 4 страница 5 ... страница 7 | страница 8
|